3d Printing In Aerospace And Defense Market Size, Share, Industry Trends and Forecast to 2033
This report provides a comprehensive analysis of the 3D Printing in Aerospace and Defense market, covering key insights, trends, and data forecasts up to 2033. It explores growth drivers, market segmentation, regional dynamics, and the competitive landscape.
Metric | Value |
---|---|
Study Period | 2023 - 2033 |
2023 Market Size | $2.30 Billion |
CAGR (2023-2033) | 8.7% |
2033 Market Size | $5.44 Billion |
Top Companies | GE Aviation, Stratasys, 3D Systems, Airbus, Lockheed Martin |
Last Modified Date | Invalid Date |
3d Printing In Aerospace And Defense Market Report (2023 - 2033)
3d Printing In Aerospace And Defense Market Overview
What is the Market Size & CAGR of 3d Printing In Aerospace And Defense market in 2033?
3d Printing In Aerospace And Defense Industry Analysis
3d Printing In Aerospace And Defense Market Segmentation and Scope
Request a custom research report for industry.
3d Printing In Aerospace And Defense Market Analysis Report by Region
Europe 3d Printing In Aerospace And Defense Market Report:
Europe is expected to witness growth from $0.67 billion in 2023 to $1.59 billion by 2033, with a strong emphasis on sustainability and innovation in aerospace technology. Countries like Germany and the UK are adopting advanced manufacturing processes, including 3D printing.Asia Pacific 3d Printing In Aerospace And Defense Market Report:
The Asia-Pacific region is anticipated to experience substantial growth in the 3D printing market for Aerospace and Defense, projected to rise from $0.44 billion in 2023 to $1.04 billion by 2033. This growth is driven by increasing aerospace production and defense expenditures in countries such as China and India, along with significant investments in 3D printing technologies.North America 3d Printing In Aerospace And Defense Market Report:
North America stands as the largest market, with a projection of growth from $0.84 billion in 2023 to $1.99 billion by 2033. The U.S. is at the forefront of adopting 3D printing technologies in military applications and commercial aerospace, driven by defense contracts and technological innovation.South America 3d Printing In Aerospace And Defense Market Report:
In South America, the market is expected to grow from $0.10 billion in 2023 to $0.24 billion by 2033. Growth in this region is slower compared to others, influenced by economic constraints, but there is potential in aerospace aviation and defense modernization projects.Middle East & Africa 3d Printing In Aerospace And Defense Market Report:
The Middle East and Africa market is projected to increase from $0.25 billion in 2023 to $0.59 billion by 2033. The growth is influenced by the region's focus on defense capabilities and advances in aerospace technology.Request a custom research report for industry.
3d Printing In Aerospace And Defense Market Analysis By Material
Global 3D Printing in Aerospace and Defense Market, By Material Market Analysis (2024 - 2033)
Materials used in the 3D printing sector include metals, polymers, and composites, with metals holding a predominant share due to their strength and durability. In 2023, metals will account for approximately $1.57 billion (68.26% share) of the market, growing to $3.72 billion (68.26% share) by 2033. Polymers and composites also play significant roles, expected to reach $1.56 billion and $0.17 billion respectively by 2033.
3d Printing In Aerospace And Defense Market Analysis By Technology
Global 3D Printing in Aerospace and Defense Market, By Technology Market Analysis (2024 - 2033)
The market is segmented by technology, with Selective Laser Melting (SLM) dominating. In 2023, SLM is valued at $1.57 billion, expanding to $3.72 billion by 2033. Fused Deposition Modeling (FDM) and Selective Laser Sintering (SLS) are also significant but with smaller market shares, projected to grow steadily over the same period.
3d Printing In Aerospace And Defense Market Analysis By Application
Global 3D Printing in Aerospace and Defense Market, By Application Market Analysis (2024 - 2033)
Applications of 3D printing encompass aerospace components, defense parts, and prototyping. Aerospace components are expected to generate $1.57 billion in 2023, growing to $3.72 billion by 2033. Defense parts are anticipated to rise from $0.66 billion to $1.56 billion in the same period, demonstrating a firm commitment to modernizing defense manufacturing.
3d Printing In Aerospace And Defense Market Analysis By Organization Size
Global 3D Printing in Aerospace and Defense Market, By Organization Size Market Analysis (2024 - 2033)
The market is also segmented by organizational size, with small and medium-sized enterprises (SMEs) commanding the highest share, at $1.87 billion, or 81.16% share, in 2023, increasing to $4.42 billion by 2033. Conversely, large enterprises are expected to grow from $0.43 billion to $1.03 billion, emphasizing a shift in how smaller firms leverage 3D technologies.
3d Printing In Aerospace And Defense Market Analysis By End User
Global 3D Printing in Aerospace and Defense Market, By End-User Market Analysis (2024 - 2033)
End-user segments consist of airlines, defense contractors, and space agencies. Airlines represent the largest share, valued at $1.57 billion and expected to reach $3.72 billion by 2033. Defense contractors are also vital, increasing from $0.66 billion to $1.56 billion, further solidifying the role of 3D printing in enhancing operational capabilities.
3d Printing In Aerospace And Defense Market Trends and Future Forecast
Request a custom research report for industry.
Global Market Leaders and Top Companies in 3d Printing In Aerospace And Defense Industry
GE Aviation:
A subsidiary of General Electric, GE Aviation leads the market with advanced additive manufacturing technologies that produce lightweight, high-strength components used in jet engines and other aerospace applications.Stratasys:
A pioneer in 3D printing technology, Stratasys provides Fused Deposition Modeling printers that are widely adopted in aerospace for prototyping and manufacturing complex parts.3D Systems:
Offering a diverse range of 3D printers and materials, 3D Systems serves both commercial aerospace and defense industries with tailored solutions for product development.Airbus:
Airbus leverages additive manufacturing in its production processes to create lightweight aircraft components, significantly reducing lead times and costs.Lockheed Martin:
A key player in defense, Lockheed Martin employs 3D printing technology to optimize parts for military applications, enhancing performance and reducing waste.We're grateful to work with incredible clients.
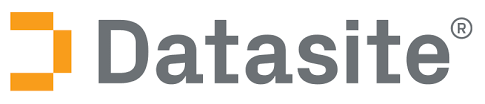
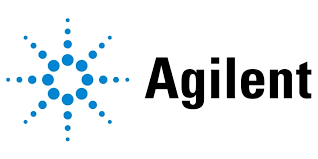

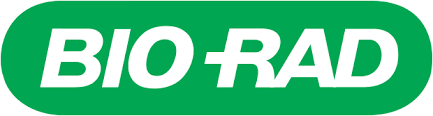
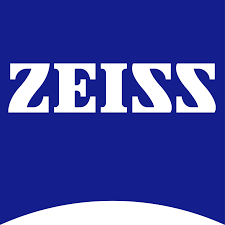
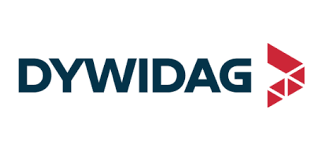
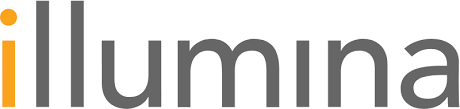

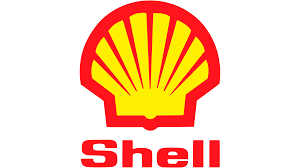
Related Industries
FAQs
What is the market size of 3D printing in aerospace and defense?
The 3D printing market in aerospace and defense is valued at approximately $2.3 billion in 2023, with a projected CAGR of 8.7% from 2023 to 2033, indicating strong growth opportunities in this sector.
What are the key market players or companies in the 3D printing in aerospace and defense industry?
Key players in the 3D printing aerospace and defense industry include major companies such as Boeing, Airbus, Lockheed Martin, and additive manufacturing firms like Stratasys and 3D Systems, driving technological advancements.
What are the primary factors driving the growth in the 3D printing in aerospace and defense industry?
The growth of the 3D printing industry in aerospace and defense is driven by the need for lightweight components, reduced manufacturing costs, rapid prototyping, customization capabilities, and increased demand for innovative designs.
Which region is the fastest Growing in the 3D printing in aerospace and defense?
The fastest-growing region in 3D printing for aerospace and defense is Europe, with a market size projected to grow from $0.67 billion in 2023 to $1.59 billion by 2033, indicating significant growth potential.
Does ConsaInsights provide customized market report data for the 3D printing in aerospace and defense industry?
Yes, ConsaInsights offers customized market report data tailored to the specific needs of clients in the 3D printing aerospace and defense industry, ensuring comprehensive insights and analysis.
What deliverables can I expect from this 3D printing in aerospace and defense market research project?
Expect deliverables such as detailed market analysis, growth projections, competitive landscape overview, segmentation insights, and regional analysis, all aimed at supporting strategic decision-making.
What are the market trends of 3D printing in aerospace and defense?
Current trends in the 3D printing aerospace and defense market include increasing adoption of metal 3D printing technologies, sustainability in manufacturing processes, and growing interest in additive production for on-demand components.