3d Printing In Oil Gas Market Size, Share, Industry Trends and Forecast to 2033
This report provides a comprehensive analysis of the 3D Printing in Oil and Gas market, covering current trends, market size, forecasts through 2033, and regional insights. It explores the industry landscape, technology impacts, and competitive dynamics to offer valuable insights to stakeholders.
Metric | Value |
---|---|
Study Period | 2023 - 2033 |
2023 Market Size | $2.30 Billion |
CAGR (2023-2033) | 7.8% |
2033 Market Size | $4.99 Billion |
Top Companies | Company A, Company B, Company C |
Last Modified Date | Invalid Date |
3d Printing In Oil Gas Market Report (2023 - 2033)
3d Printing In Oil Gas Market Overview
What is the Market Size & CAGR of 3d Printing In Oil Gas market in 2023?
3d Printing In Oil Gas Industry Analysis
3d Printing In Oil Gas Market Segmentation and Scope
Request a custom research report for industry.
3d Printing In Oil Gas Market Analysis Report by Region
Europe 3d Printing In Oil Gas Market Report:
In Europe, the market is forecasted to expand from USD 0.57 million in 2023 to USD 1.24 million in 2033. The region is characterized by strict regulations and high standards for manufacturing processes, creating a conducive environment for 3D printing innovations.Asia Pacific 3d Printing In Oil Gas Market Report:
The Asia Pacific region is expected to witness growth from USD 0.50 million in 2023 to USD 1.09 million in 2033. The rising investments in oil exploration and production activities, coupled with technological advancements, are pivotal drivers of this growth.North America 3d Printing In Oil Gas Market Report:
North America is anticipated to grow significantly from USD 0.75 million in 2023 to USD 1.63 million in 2033, driven by high investments in R&D and the early adoption of 3D printing technologies among top oil and gas companies.South America 3d Printing In Oil Gas Market Report:
In South America, the market is projected to grow from USD 0.16 million in 2023 to USD 0.34 million in 2033. This growth is fueled by the increasing adoption of advanced manufacturing technologies in local oil and gas operations.Middle East & Africa 3d Printing In Oil Gas Market Report:
The Middle East and Africa are expected to grow from USD 0.32 million in 2023 to USD 0.69 million in 2033. The region's increasing focus on technological advancements to enhance oil recovery rates supports this growth trajectory.Request a custom research report for industry.
3d Printing In Oil Gas Market Analysis By Technology
Global 3D Printing in Oil & Gas Market, By Technology Market Analysis (2024 - 2033)
Key technologies in use include Fused Deposition Modeling (FDM), Selective Laser Sintering (SLS), and Stereolithography (SLA). FDM dominates the market with a size of USD 1.44 million in 2023, expected to grow to USD 3.13 million in 2033. SLS and SLA also exhibit promising growth, capitalizing on the demand for high-precision components.
3d Printing In Oil Gas Market Analysis By Application Field
Global 3D Printing in Oil & Gas Market, By Application Field Market Analysis (2024 - 2033)
The application field segmentation reveals key areas such as upstream, midstream, and downstream processes. The upstream segment leads with USD 1.44 million in 2023, significantly growing to USD 3.13 million by 2033, driven by the need for rapid prototyping and spare parts manufacturing.
3d Printing In Oil Gas Market Analysis By Material
Global 3D Printing in Oil & Gas Market, By Material Market Analysis (2024 - 2033)
Materials used in 3D printing in this sector include metals, polymers, and ceramics. Metals, especially, are projected to grow from USD 1.44 million in 2023 to USD 3.13 million by 2033, owing to their strength and durability in oil and gas applications.
3d Printing In Oil Gas Market Analysis By End User
Global 3D Printing in Oil & Gas Market, By End User Market Analysis (2024 - 2033)
End-users comprise exploration companies, drilling service firms, and equipment manufacturers. Exploration companies, with a significant market presence, are expected to continue leading through 2033, supported by the increased use of custom components and quick turnaround times.
3d Printing In Oil Gas Market Analysis By Benefit
Global 3D Printing in Oil & Gas Market, By Benefit Market Analysis (2024 - 2033)
The benefits segment highlights cost savings, time efficiency, and design freedom as critical factors for adoption. Cost savings dominate the market, representing USD 1.44 million in 2023 and forecasted to reach USD 3.13 million by 2033. Companies are increasingly recognizing the potential of 3D printing to reduce material waste and lead times.
3d Printing In Oil Gas Market Trends and Future Forecast
Request a custom research report for industry.
Global Market Leaders and Top Companies in 3d Printing In Oil Gas Industry
Company A:
A leading provider of additive manufacturing solutions, focusing on advanced 3D printing technologies for the oil and gas sector, enhancing operational efficiencies.Company B:
Specializes in polymer-based 3D printing applications, providing solutions that cater to the prototyping and custom component manufacturing needs in the oil and gas industry.Company C:
Involved in the development of metallic 3D printing processes aimed at producing high-strength components for deep-sea exploration applications.We're grateful to work with incredible clients.
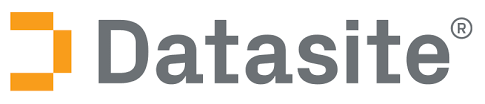
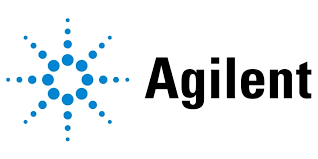

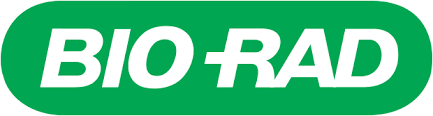
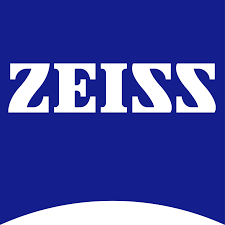
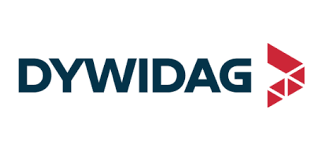
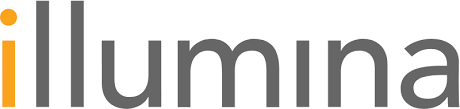

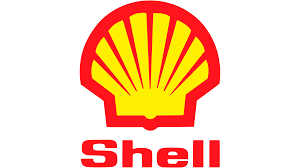
Related Industries
FAQs
What is the market size of 3D printing in oil and gas?
The 3D Printing in Oil and Gas market is valued at approximately $2.3 billion in 2023 and is projected to grow at a CAGR of 7.8% until 2033.
What are the key market players or companies in this industry?
Key players in the 3D printing in oil and gas sector include major companies and technology providers specializing in additive manufacturing solutions tailored for the industry’s unique needs.
What are the primary factors driving the growth in the 3D printing industry?
The growth is primarily driven by demand for cost savings, improved design freedom, enhanced time efficiency, and the ability to produce complex components rapidly.
Which region is the fastest Growing in the 3D printing market?
The Asia Pacific region is anticipated to be the fastest-growing market, increasing from $0.50 billion in 2023 to $1.09 billion by 2033.
Does ConsaInsights provide customized market report data for the 3D printing industry?
Yes, ConsaInsights offers customized market research reports tailored to specific needs within the 3D printing industry, ensuring clients receive relevant insights.
What deliverables can I expect from this market research project?
Deliverables typically include comprehensive market analysis, trends, pricing strategies, competitive landscape, and sector-specific insights relevant to 3D printing in oil and gas.
What are the market trends of 3D printing in oil and gas?
Current trends include increased adoption of additive manufacturing for spare parts and tooling, advancements in technology like FDM and SLS, and a focus on sustainability and efficiency.