3d Printing Metal Market Size, Share, Industry Trends and Forecast to 2033
This report provides a comprehensive analysis of the 3D printing metal market from 2023 to 2033, detailing current trends, market conditions, forecasts, and segmented analyses across regions and application categories.
Metric | Value |
---|---|
Study Period | 2023 - 2033 |
2023 Market Size | $2.50 Billion |
CAGR (2023-2033) | 25% |
2033 Market Size | $26.69 Billion |
Top Companies | Stratasys Ltd., 3D Systems Corporation, EOS GmbH, SLM Solutions Group AG, Markforged, Inc. |
Last Modified Date | Invalid Date |
3d Printing Metal Market Report (2023 - 2033)
3D Printing Metal Market Overview
What is the Market Size & CAGR of 3D Printing Metal market in 2033?
3D Printing Metal Industry Analysis
3D Printing Metal Market Segmentation and Scope
Request a custom research report for industry.
3D Printing Metal Market Analysis Report by Region
Europe 3d Printing Metal Market Report:
The European market is projected to rise from $0.79 billion in 2023 to $8.40 billion by 2033, spurred by advancements in design and manufacturing capabilities and a strong regulatory framework supporting innovative technologies.Asia Pacific 3d Printing Metal Market Report:
The Asia-Pacific region is expected to experience rapid growth, with the market projected to increase from $0.45 billion in 2023 to $4.84 billion in 2033. This growth is driven by rising investments in manufacturing technologies and an increasing number of startups focusing on advanced 3D metal printing solutions.North America 3d Printing Metal Market Report:
North America, particularly the U.S., holds the largest market share, expected to grow from $0.89 billion in 2023 to $9.45 billion in 2033. This is largely due to its established manufacturing base and the presence of key players actively investing in the latest technologies.South America 3d Printing Metal Market Report:
In South America, the market size is anticipated to grow from $0.17 billion in 2023 to $1.86 billion by 2033. The region's growth can be attributed to burgeoning interest in applying 3D printing technologies to local industries, particularly in automotive and consumer goods.Middle East & Africa 3d Printing Metal Market Report:
The Middle East and Africa market, still emerging, is expected to grow from $0.20 billion in 2023 to $2.13 billion in 2033. The region's oil and gas sector is increasingly looking to 3D printing to streamline production processes and reduce reliance on imports.Request a custom research report for industry.
3d Printing Metal Market Analysis By Material
Global 3D Printing Metal Market, By Material Market Analysis (2024 - 2033)
The 3D printing metal market is significantly influenced by material types. Titanium dominates the market, valued at $1.35 billion in 2023, and is expected to increase to $14.43 billion by 2033, holding a 54.06% market share. Other materials like steel and aluminum also contribute, with steel projected to grow from $0.60 billion to $6.42 billion, accounting for 24.05% share.
3d Printing Metal Market Analysis By Technology
Global 3D Printing Metal Market, By Technology Market Analysis (2024 - 2033)
Technological advancements play a substantial role in shaping the 3D printing metal landscape. Powder Bed Fusion is the leading technology segment, expected to grow from $1.35 billion in 2023 to $14.43 billion by 2033, representing a 54.06% share. Direct Energy Deposition and Binder Jetting follow, with respective market sizes of $0.60 billion and $0.29 billion in 2023.
3d Printing Metal Market Analysis By Application
Global 3D Printing Metal Market, By Application Market Analysis (2024 - 2033)
Application sectors exhibit varying growth patterns, with aerospace leading at $1.19 billion in 2023, projected to reach $12.76 billion by 2033, capturing a 47.8% share. Automotive and healthcare sectors also show promising growth, with automotive increasing from $0.52 billion to $5.53 billion.
3d Printing Metal Market Analysis By End User
Global 3D Printing Metal Market, By End-User Market Analysis (2024 - 2033)
End-user analysis reveals diverse demand across sectors. Large enterprises, dominating the space with a market size projected to grow from $1.66 billion to $17.77 billion, assert control with a 66.59% share. Small and medium enterprises are gradually increasing their presence, with significant growth expected.
3d Printing Metal Market Analysis By Geography
Global 3D Printing Metal Market, By Geography Segmentation Market Analysis (2024 - 2033)
Geographically, North America continues to be the strongest player, followed by Europe, highlighting a balanced approach between established markets and emerging regions. Continuous innovations drive these markets and provide significant revenue opportunities.
3D Printing Metal Market Trends and Future Forecast
Request a custom research report for industry.
Global Market Leaders and Top Companies in 3D Printing Metal Industry
Stratasys Ltd.:
A leading manufacturer of 3D printers that actively develops solutions for metal printing, pushing innovations in materials and technologies.3D Systems Corporation:
Known for their comprehensive suite of 3D printing solutions, including advanced metal printing systems and materials used in various industries.EOS GmbH:
A global pioneer in the field of industrial 3D printing, offering advanced solutions for metal-additive manufacturing.SLM Solutions Group AG:
A leader in metal 3D printing technology, SLM Solutions provides innovative systems geared towards serial production.Markforged, Inc.:
Known for pioneering metal 3D printers suitable for various engineering applications, focusing on providing robust and reliable manufacturing solutions.We're grateful to work with incredible clients.
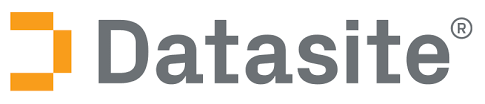
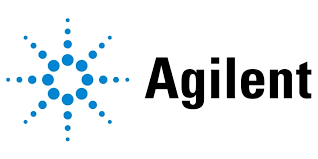

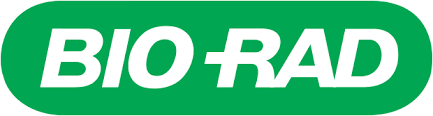
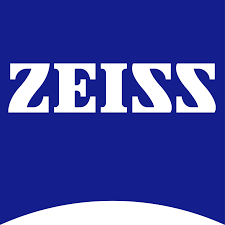
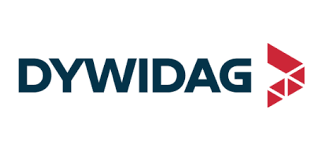
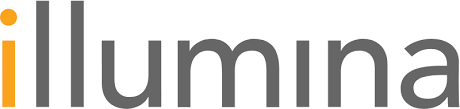

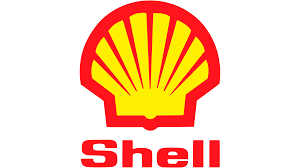
Related Industries
FAQs
What is the market size of 3D-Printing-Metal?
The global 3D-Printing-Metal market is currently valued at approximately $2.5 billion and is projected to grow at a CAGR of 25% through 2033, indicating significant expansion and opportunities in this innovative industry.
What are the key market players or companies in this 3D-Printing-Metal industry?
Key players in the 3D-Printing-Metal industry include Stratasys, 3D Systems, GE Additive, EOS GmbH, and Desktop Metal, which lead in technological advancements and adoption of metal 3D printing solutions.
What are the primary factors driving the growth in the 3D-Printing-Metal industry?
Growth in the 3D-Printing-Metal industry is driven by factors such as increasing demand for complex geometries, advancements in additive manufacturing technologies, and the need for lightweight materials across sectors like aerospace and automotive.
Which region is the fastest Growing in the 3D-Printing-Metal?
North America is the fastest-growing region in the 3D-Printing-Metal market, with market size projected to increase from $0.89 billion in 2023 to $9.45 billion by 2033, driven by innovation and R&D investments.
Does ConsaInsights provide customized market report data for the 3D-Printing-Metal industry?
Yes, ConsaInsights offers customized market reports tailored to the specific needs and inquiries of clients, providing detailed insights into the 3D-Printing-Metal industry.
What deliverables can I expect from this 3D-Printing-Metal market research project?
Key deliverables from this market research project include comprehensive market analysis, competitive landscape insights, regional breakdown data, and growth forecasts, ensuring informed decision-making.
What are the market trends of 3D-Printing-Metal?
Market trends in 3D-Printing-Metal include increased adoption of advanced materials like titanium and steel, growth in applications across aerospace and automotive sectors, and shifts towards sustainable manufacturing practices.