Aero Engine Composites Market Size, Share, Industry Trends and Forecast to 2033
This report covers a comprehensive analysis of the Aero Engine Composites market, featuring insights on market dynamics, growth forecasts from 2023 to 2033, and key trends impacting the industry. It provides detailed data on market size, segmentation, regional performance, and leading players.
Metric | Value |
---|---|
Study Period | 2023 - 2033 |
2023 Market Size | $1.50 Billion |
CAGR (2023-2033) | 6.0% |
2033 Market Size | $2.72 Billion |
Top Companies | General Electric, Rolls Royce, Honeywell , Boeing |
Last Modified Date | 27 February 2025 |
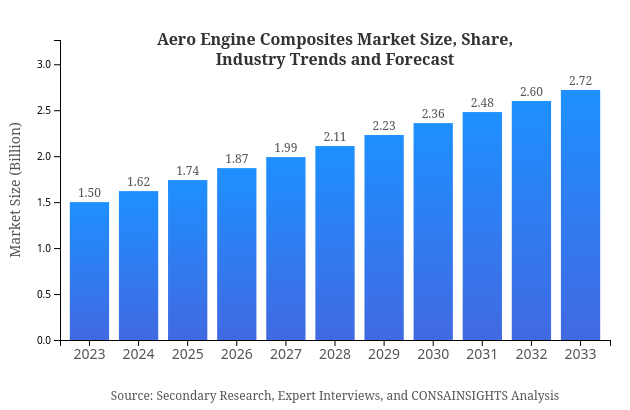
Aero Engine Composites Market Overview
What is the Market Size & CAGR of Aero Engine Composites market in 2023?
Aero Engine Composites Industry Analysis
Aero Engine Composites Market Segmentation and Scope
Request a custom research report for industry.
Aero Engine Composites Market Analysis Report by Region
Europe Aero Engine Composites Market Report:
The European market is projected to grow from USD 0.40 billion in 2023 to USD 0.73 billion by 2033. The region leads in innovation and technology adoption in the aviation sector, fostering growth within the Aero Engine Composites market.Asia Pacific Aero Engine Composites Market Report:
In 2023, the Aero Engine Composites market in Asia Pacific is valued at USD 0.30 billion, projected to grow to USD 0.54 billion by 2033. This growth is fueled by rising air traffic in developing economies, increased local manufacturing capabilities, and government initiatives supporting aerospace development.North America Aero Engine Composites Market Report:
North America is crucial in the Aero Engine Composites market, with a size of USD 0.55 billion in 2023, expected to increase to USD 0.99 billion in 2033. The advanced aerospace sector, characterized by established manufacturers and R&D activities, drives significant demand for composite materials.South America Aero Engine Composites Market Report:
The South American market for Aero Engine Composites is valued at USD 0.15 billion in 2023, with a forecasted growth to USD 0.27 billion by 2033. The region's growth is supported by rising investments in aviation infrastructure and increasing demand for new commercial aircraft.Middle East & Africa Aero Engine Composites Market Report:
The Aero Engine Composites market in the Middle East and Africa is anticipated to grow from USD 0.10 billion in 2023 to USD 0.19 billion by 2033. Expansion in the regional aviation sector and increased military spending are significant growth drivers.Request a custom research report for industry.
Aero Engine Composites Market Analysis By Material Type
Global Aero Engine Composites Market, By Material Type Market Analysis (2024 - 2033)
The market is predominantly driven by carbon fiber composites, which are valued at USD 1.03 billion in 2023, with an increase to USD 1.87 billion by 2033. Glass fiber composites account for USD 0.35 billion and expected to grow to USD 0.64 billion. Aramid fiber composites remain less critical, reflecting a market size from USD 0.12 billion to USD 0.22 billion within the same period.
Aero Engine Composites Market Analysis By Engine Type
Global Aero Engine Composites Market, By Engine Type Market Analysis (2024 - 2033)
Within the Aero Engine Composites market, turbofan engines dominate, with a projected growth from USD 1.03 billion in 2023 to USD 1.87 billion by 2033. Turbojet engines are valued at USD 0.35 billion, showing growth to USD 0.64 billion. Turboprop engines represent a smaller share ranging from USD 0.12 billion to USD 0.22 billion.
Aero Engine Composites Market Analysis By Application
Global Aero Engine Composites Market, By Application Market Analysis (2024 - 2033)
The segment for commercial aviation leads with a market size of USD 1.03 billion in 2023, anticipated to grow to USD 1.87 billion by 2033. Military aviation and unmanned aerial vehicles follow, with respective sizes of USD 0.35 billion to USD 0.64 billion and USD 0.12 billion to USD 0.22 billion.
Aero Engine Composites Market Analysis By Manufacturing Method
Global Aero Engine Composites Market, By Manufacturing Method Market Analysis (2024 - 2033)
Current manufacturing methods, such as the Hand Layup Process, dominate with a market size of USD 1.03 billion in 2023, projected to reach USD 1.87 billion by 2033. The Resin Infusion Process and Pultrusion Process are smaller segments valued at USD 0.35 billion and USD 0.12 billion respectively, with growth prospects confirming increased market interest.
Aero Engine Composites Market Analysis By End User
Global Aero Engine Composites Market, By End-User Market Analysis (2024 - 2033)
The Aero Engine Composites market sees significant demand from aerospace manufacturers, with sizes projected to grow from USD 1.03 billion to USD 1.87 billion. Airlines contribute USD 0.35 billion growing to USD 0.64 billion, while the Maintenance, Repair, and Operations (MRO) segment increases from USD 0.12 billion to USD 0.22 billion.
Aero Engine Composites Market Trends and Future Forecast
Request a custom research report for industry.
Global Market Leaders and Top Companies in Aero Engine Composites Industry
General Electric:
A leading company in manufacturing aircraft engines and providing technology innovations in composite materials for better performance.Rolls Royce:
Specializes in developing cutting-edge aerospace technologies focusing on high-performance materials, including composites.Honeywell :
Focuses on developing advanced materials and solutions for the aerospace sector, enhancing engine efficiency through innovative composite use.Boeing :
Employs advanced composites in its aircraft designs to improve performance and reduce weight significantly.We're grateful to work with incredible clients.
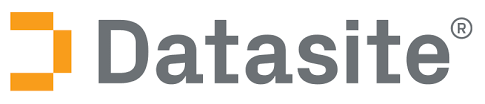
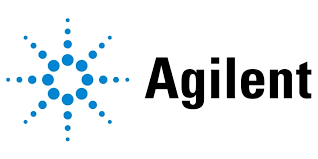

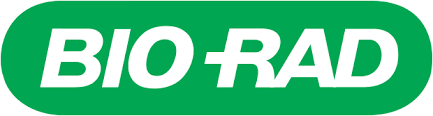
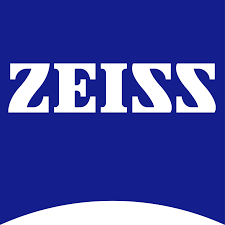
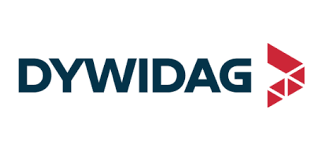
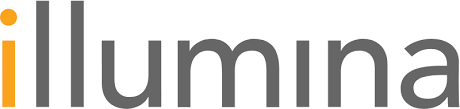

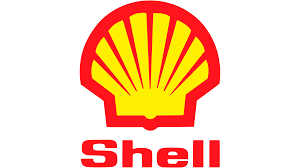
Related Industries
FAQs
What is the market size of aero Engine Composites?
The aero-engine composites market is projected to reach $1.5 billion by 2033, with a compound annual growth rate (CAGR) of 6.0%. This growth reflects rising demand for lightweight and high-performance materials in aerospace applications.
What are the key market players or companies in the aero Engine Composites industry?
Key players in the aero-engine composites market include major aerospace manufacturers and component suppliers, involved in producing advanced composite materials tailored for specific applications in commercial and military aviation.
What are the primary factors driving the growth in the aero Engine Composites industry?
Significant factors propelling growth include advancements in composite materials technology, increasing fuel efficiency requirements, and the growing demand for lightweight components in aircraft to enhance performance and reduce emissions.
Which region is the fastest Growing in the aero Engine Composites?
The North America region is the fastest-growing market for aero-engine composites, expected to grow from $0.55 billion in 2023 to $0.99 billion by 2033, largely driven by its established aerospace industry and innovation.
Does ConsaInsights provide customized market report data for the aero Engine Composites industry?
Yes, ConsaInsights offers customized market report data tailored to client-specific needs in the aero-engine composites industry, allowing stakeholders to make informed decisions based on detailed analysis and market insights.
What deliverables can I expect from this aero Engine Composites market research project?
Deliverables include comprehensive market analysis reports, segmentation data, competitive landscape assessments, and trend analysis covering various aspects of the aero-engine composites industry for strategic planning.
What are the market trends of aero Engine Composites?
Current trends in the aero-engine composites market include innovations in carbon fiber technologies, increasing applications in turbofan and turbojet engines, and a shift toward sustainable materials to meet global aviation regulations.