Aluminum Casting Market Size, Share, Industry Trends and Forecast to 2033
This report delves into the Aluminum Casting market, offering detailed insights and data on market size, growth trends, and regional dynamics from 2023 to 2033. The analysis encompasses various segments, industry leaders, and technology advances influencing the market landscape.
Metric | Value |
---|---|
Study Period | 2023 - 2033 |
2023 Market Size | $12.00 Billion |
CAGR (2023-2033) | 5.8% |
2033 Market Size | $21.37 Billion |
Top Companies | Nemak, Alcoa Corporation, HawkeyePedershaab, Magna International |
Last Modified Date | Invalid Date |
Aluminum Casting Market Report (2023 - 2033)
Aluminum Casting Market Overview
What is the Market Size & CAGR of Aluminum Casting market in 2023?
Aluminum Casting Industry Analysis
Aluminum Casting Market Segmentation and Scope
Request a custom research report for industry.
Aluminum Casting Market Analysis Report by Region
Europe Aluminum Casting Market Report:
In Europe, the market will likely increase from $3.09 billion in 2023 to $5.51 billion by 2033, driven by stringent emissions regulations incentivizing the use of lightweight materials in various industries, especially automotive and aerospace.Asia Pacific Aluminum Casting Market Report:
The Asia Pacific region is projected to grow from $2.45 billion in 2023 to $4.36 billion by 2033, driven by rapid industrialization and expansion in the automotive sector. Countries like China and India are significant contributors, with a growing base of automotive manufacturers pushing demand for aluminum components.North America Aluminum Casting Market Report:
North America is forecasted to grow from $3.94 billion in 2023 to $7.02 billion by 2033, supported by a mature automotive industry and a shift towards electric vehicle production which demands lightweight components.South America Aluminum Casting Market Report:
In South America, the market is estimated to expand from $1.19 billion in 2023 to $2.12 billion in 2033. The growth is primarily attributed to increasing construction activities and automotive production, alongside government initiatives enhancing manufacturing capabilities.Middle East & Africa Aluminum Casting Market Report:
The Middle East and Africa market is expected to experience growth from $1.32 billion in 2023 to $2.36 billion by 2033, driven by infrastructural development and rising local manufacturing capabilities in automotive and aerospace sectors.Request a custom research report for industry.
Aluminum Casting Market Analysis By Product
Global Aluminum Casting Market, By Product Type Market Analysis (2024 - 2033)
The Aluminum Casting market by product type encompasses various processes including die casting, sand casting, gravity casting, pressure casting, and investment casting. In 2023, the die casting segment accounts for the largest share at $7.25 billion, projected to reach $12.91 billion by 2033. The pressure casting segment follows with a size of $3.27 billion in 2023, expected to grow to $5.82 billion by 2033. Advanced casting techniques are gaining prominence, enhancing automation and precision in production.
Aluminum Casting Market Analysis By Application
Global Aluminum Casting Market, By Application Market Analysis (2024 - 2033)
Applications of aluminum casting are widespread, with dominant sectors including automotive, aerospace, electronics, and construction. The automotive application leads with a market size of $6.23 billion in 2023, projected to reach $11.09 billion by 2033. The requirements for lightweight materials in this sector foster continuous growth. Aerospace applications are also significant, increasing from $2.82 billion to $5.03 billion during the same period.
Aluminum Casting Market Analysis By Technology
Global Aluminum Casting Market, By Technology Market Analysis (2024 - 2033)
The industry is moving towards advanced casting technologies that enhance efficiency and output quality. Conventional casting techniques retain a significant market share of 81.2% in 2023, but innovative techniques are expected to grow from $2.26 billion in 2023 to $4.02 billion by 2033, driven by market demands for sustainable practices.
Aluminum Casting Market Analysis By End User
Global Aluminum Casting Market, By End-User Industry Market Analysis (2024 - 2033)
Major end-users include automotive manufacturers, construction, and electrical sectors. The automotive industry holds a commanding market share of 51.88% due to the increasing push for eco-friendly and energy-efficient vehicles. Construction applications also represent a growing sector, driven by rising infrastructure projects and housing demand.
Aluminum Casting Market Analysis By Process
Global Aluminum Casting Market, By Casting Process Market Analysis (2024 - 2033)
The market is segmented by casting processes including die casting, sand casting, gravity casting, pressure casting, and investment casting. Each process serves unique industry needs, with die casting and pressure casting being the leading methods due to their efficiency and high precision in producing intricate designs.
Aluminum Casting Market Trends and Future Forecast
Request a custom research report for industry.
Global Market Leaders and Top Companies in Aluminum Casting Industry
Nemak:
Nemak is a leading global manufacturer of aluminum components, focusing on innovation and sustainable practices. The company plays a pivotal role in the automotive sector, providing lightweight and high-performance castings.Alcoa Corporation:
Alcoa is a major player in aluminum production and manufacturing, highly recognized for its advanced metal and material technologies. Their commitment to sustainability enhances their position in the aluminum casting industry.HawkeyePedershaab:
Specializing in casting techniques, HawkeyePedershaab provides cutting-edge technology and solutions for the building materials industry, particularly in pre-cast concrete products.Magna International:
Magna International is a diversified automotive supplier, offering a wide range of vehicle components while leading innovations in aluminum die casting to optimize vehicle performance.We're grateful to work with incredible clients.
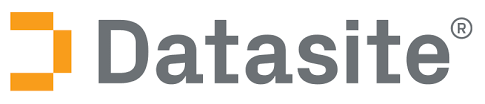
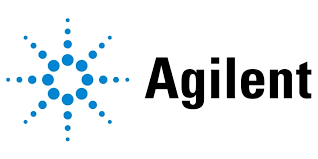

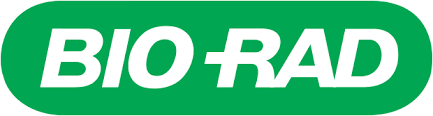
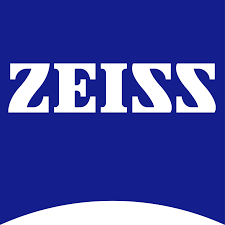
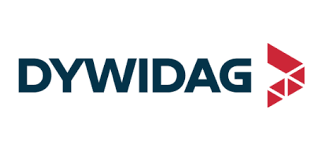
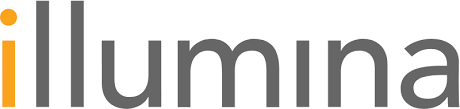

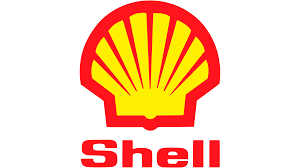
Related Industries
FAQs
What is the market size of aluminum Casting?
The global aluminum casting market size is projected to be $12 billion in 2023 and is expected to grow at a CAGR of 5.8% through 2033, reflecting increasing demand across multiple industries.
What are the key market players or companies in this aluminum Casting industry?
Key players in the aluminum casting industry include Alcoa Corporation, Dynacast, NovaCast, and Øveraasen. Their innovative practices and emphasis on quality and sustainability drive competition and advancements in the market.
What are the primary factors driving the growth in the aluminum Casting industry?
Growth in the aluminum casting industry is driven by increased demand in automotive and aerospace sectors, technological advancements, lightweight material preferences, and stringent regulatory standards aimed at sustainability.
Which region is the fastest Growing in the aluminum Casting?
The North America region currently holds significant market shares and is the fastest-growing area, projecting market growth from $3.94 billion in 2023 to $7.02 billion by 2033, driven by robust automotive and aerospace industries.
Does ConsaInsights provide customized market report data for the aluminum Casting industry?
Yes, ConsaInsights offers customized market report data catering to specific client needs in the aluminum casting industry, allowing for tailored insights and analysis based on individual business requirements.
What deliverables can I expect from this aluminum Casting market research project?
Deliverables from the aluminum casting market research project typically include detailed market analysis reports, trend forecasts, competitive landscape assessments, and segmented insights into regional and application-specific data.
What are the market trends of aluminum Casting?
Trends in the aluminum casting market include the rising adoption of advanced casting techniques, a shift towards sustainability, increasing automation in production processes, and greater application of aluminum in lightweight automotive design.