Aluminum Parts Gravity Die Casting Market Size, Share, Industry Trends and Forecast to 2033
This report provides an in-depth analysis of the aluminum parts gravity die casting market, including detailed insights on market trends, sizes, and forecasts from 2023 to 2033. It covers key segments and regional analyses to offer a comprehensive understanding of industry dynamics.
Metric | Value |
---|---|
Study Period | 2023 - 2033 |
2023 Market Size | $5.40 Billion |
CAGR (2023-2033) | 6.8% |
2033 Market Size | $10.61 Billion |
Top Companies | Nemak, Continental Structural Plastics, Aluminium Die Casting Company |
Last Modified Date | Invalid Date |
Aluminum Parts Gravity Die Casting Market Report (2023 - 2033)
Aluminum Parts Gravity Die Casting Market Overview
What is the Market Size & CAGR of Aluminum Parts Gravity Die Casting market in 2023?
Aluminum Parts Gravity Die Casting Industry Analysis
Aluminum Parts Gravity Die Casting Market Segmentation and Scope
Request a custom research report for industry.
Aluminum Parts Gravity Die Casting Market Analysis Report by Region
Europe Aluminum Parts Gravity Die Casting Market Report:
The European market is a significant player, valued at $1.87 billion in 2023 and expected to reach $3.67 billion by 2033. The industry's growth is supported by stringent regulations favoring lightweight and fuel-efficient vehicles, propelling demand for aluminum parts.Asia Pacific Aluminum Parts Gravity Die Casting Market Report:
In 2023, the Asia Pacific region is valued at $1.00 billion, projected to grow to $1.97 billion by 2033, driven by rising automotive production and a strong industrial base. Countries like China and India are becoming significant contributors due to their expanding manufacturing capacities and investment in infrastructure.North America Aluminum Parts Gravity Die Casting Market Report:
North America stands at $1.76 billion in 2023, with forecasts indicating growth to $3.47 billion by 2033. The region benefits from technological advancements in manufacturing and strong demand from the automotive and aerospace sectors.South America Aluminum Parts Gravity Die Casting Market Report:
South America's aluminum parts gravity die casting market, valued at $0.28 billion in 2023, is expected to reach $0.55 billion by 2033. Growth is attributed to increased demand for automotive components as the region's automotive industry develops.Middle East & Africa Aluminum Parts Gravity Die Casting Market Report:
The Middle East and Africa market is projected to grow from $0.49 billion in 2023 to $0.95 billion by 2033 due to rising infrastructure projects and industrialization, leading to increased demand for aluminum components.Request a custom research report for industry.
Aluminum Parts Gravity Die Casting Market Analysis By Material Grade
Global Aluminum Parts Gravity Die Casting Market, By Material Grade Market Analysis (2024 - 2033)
The aluminum parts gravity die casting market is segmented into high strength aluminum alloys and standard grade alloys. In 2023, high strength alloys dominate with a market size of $4.32 billion (80.08% share), expected to reach $8.50 billion by 2033. Standard grade alloys, valued at $1.08 billion in 2023 (19.92% share), are projected to grow to $2.11 billion.
Aluminum Parts Gravity Die Casting Market Analysis By Product Type
Global Aluminum Parts Gravity Die Casting Market, By Product Type Market Analysis (2024 - 2033)
The market by product type includes automotive parts, industrial parts, and consumer products. Automotive parts lead the segment with $3.38 billion and a 62.56% market share in 2023, projected to grow to $6.64 billion by 2033. Industrial parts and consumer products, valued at $1.10 billion and $0.93 billion, respectively, show steady growth potential.
Aluminum Parts Gravity Die Casting Market Analysis By Process Type
Global Aluminum Parts Gravity Die Casting Market, By Process Type Market Analysis (2024 - 2033)
The analysis by process type highlights hot chamber die casting and cold chamber die casting methods. Hot chamber die casting is the preferred method, contributing $4.32 billion in 2023 (80.08% share) and expected to grow to $8.50 billion. Cold chamber die casting, with a modest $1.08 billion value in 2023 (19.92% share), is anticipated to reach $2.11 billion.
Aluminum Parts Gravity Die Casting Market Analysis By End User Industry
Global Aluminum Parts Gravity Die Casting Market, By End User Industry Market Analysis (2024 - 2033)
The end-user industry segmentation reveals strong demand from automotive, aerospace, and electronics sectors. The automotive industry accounts for $3.38 billion and a 62.56% share in 2023, with growth expected up to $6.64 billion by 2033. Aerospace parts are valued at $1.10 billion in 2023 and projected to grow significantly as innovation in aircraft design continues.
Aluminum Parts Gravity Die Casting Market Analysis By Application
Global Aluminum Parts Gravity Die Casting Market, By Application Market Analysis (2024 - 2033)
Applications of aluminum parts gravity die casting include automotive, aerospace, and electronic devices. Automotive applications lead the market with $3.38 billion (62.56% share), expected to see continuous growth. Aerospace and electronics follow, highlighting the versatility and adaptability of aluminum in various high-tech applications.
Aluminum Parts Gravity Die Casting Market Trends and Future Forecast
Request a custom research report for industry.
Global Market Leaders and Top Companies in Aluminum Parts Gravity Die Casting Industry
Nemak:
A global leader in aluminum engine components, Nemak specializes in die-casting technologies and is focused on developing innovative solutions for the automotive industry.Continental Structural Plastics:
This company is known for its advanced composite solutions and aluminum die-casting technologies, serving various industries including automotive and aerospace.Aluminium Die Casting Company:
Specializing in aluminum die casting, this company offers a range of products across multiple sectors, including automotive, aerospace, and consumer goods.We're grateful to work with incredible clients.
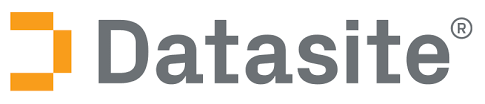
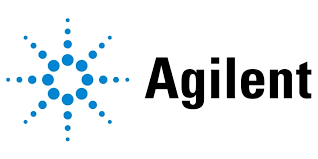

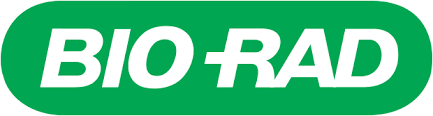
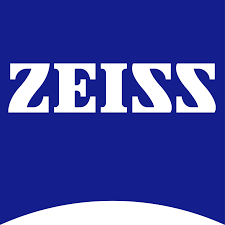
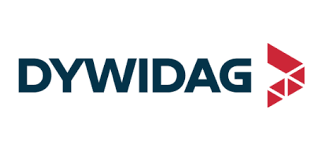
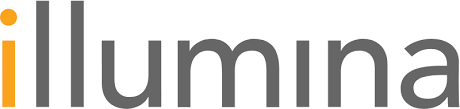

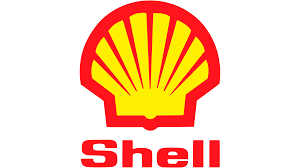
Related Industries
FAQs
What is the market size of aluminum parts gravity die casting?
The global aluminum parts gravity die casting market is valued at approximately $5.4 billion in 2023. It is projected to grow at a CAGR of 6.8%, reaching a substantial size by 2033.
What are the key market players or companies in the aluminum parts gravity die casting industry?
Key players in the aluminum parts gravity die casting industry include companies specializing in die casting technology, aluminum alloy production, and sectors such as automotive, aerospace, and electronics, driving market competitiveness and innovation.
What are the primary factors driving the growth in the aluminum parts gravity die casting industry?
The growth in the aluminum parts gravity die casting industry is primarily driven by increasing demand for lightweight and durable components in automotive and aerospace sectors, alongside innovations in casting technologies that enhance efficiency and product quality.
Which region is the fastest Growing in the aluminum parts gravity die casting?
The fastest-growing region in the aluminum parts gravity die casting market is Europe, with market size projected to grow from $1.87 billion in 2023 to $3.67 billion by 2033, reflecting increasing industrial activities and demand for precision components.
Does ConsaInsights provide customized market report data for the aluminum parts gravity die casting industry?
Yes, ConsaInsights offers customized market report data tailored to specific needs in the aluminum parts gravity die casting industry, allowing clients to gain detailed insights into market dynamics and trends relevant to their strategic goals.
What deliverables can I expect from this aluminum parts gravity die casting market research project?
From the aluminum parts gravity die casting market research project, expect comprehensive reports detailing market size, growth forecasts, competitive analysis, segment data, regional insights, and emerging trends, designed to support investment and strategic planning.
What are the market trends of aluminum parts gravity die casting?
Current market trends in aluminum parts gravity die casting include an increasing focus on sustainability, advancements in automation, and rising preference for high-strength aluminum alloys across automotive and electronics industries, enhancing product performance and reducing environmental impact.