Asia Middle East Automotive Tooling Molds Market Size, Share, Industry Trends and Forecast to 2033
This report provides an extensive analysis of the Asia Middle East Automotive Tooling Molds market, offering insights on market dynamics, growth forecasts, and regional performance from 2023 to 2033.
Metric | Value |
---|---|
Study Period | 2023 - 2033 |
2023 Market Size | $3.80 Billion |
CAGR (2023-2033) | 6.7% |
2033 Market Size | $7.40 Billion |
Top Companies | Haas Automation, Inc., Mold-Masters Limited, BASF SE, Alpine Engineering & Tooling, Inc. |
Last Modified Date | Invalid Date |
Asia Middle East Automotive Tooling Molds Market Report (2023 - 2033)
Asia Middle East Automotive Tooling Molds Market Overview
What is the Market Size & CAGR of Asia Middle East Automotive Tooling Molds market in 2023?
Asia Middle East Automotive Tooling Molds Industry Analysis
Asia Middle East Automotive Tooling Molds Market Segmentation and Scope
Request a custom research report for industry.
Asia Middle East Automotive Tooling Molds Market Analysis Report by Region
Europe Asia Middle East Automotive Tooling Molds Market Report:
In Europe, the market is valued at $1.29 billion in 2023, expected to rise to $2.50 billion by 2033. Strong regulations for emissions and sustainability are boosting investments in tooling for electric and hybrid vehicles.Asia Pacific Asia Middle East Automotive Tooling Molds Market Report:
In 2023, the Asia Pacific automotive tooling molds market is valued at approximately $0.70 billion, projected to grow to $1.35 billion by 2033. This growth is attributed to rising automotive production in countries like China, India, and Japan, along with an increasing focus on innovation in manufacturing.North America Asia Middle East Automotive Tooling Molds Market Report:
The North American segment is estimated at $1.32 billion in 2023, with forecasts of reaching $2.56 billion by 2033. The U.S. is a key driver, supported by its established automotive industry and rising demand for electric vehicles.South America Asia Middle East Automotive Tooling Molds Market Report:
The South American market for automotive tooling molds was valued at $0.06 billion in 2023 and is expected to reach $0.12 billion by 2033. The growth is moderate due to lower vehicle production compared to other regions, though investments in manufacturing are gradually increasing.Middle East & Africa Asia Middle East Automotive Tooling Molds Market Report:
The Middle East and Africa market is projected to grow from $0.44 billion in 2023 to $0.86 billion by 2033. This growth is fueled by increasing investments in automotive manufacturing, particularly in the Gulf countries.Request a custom research report for industry.
Asia Middle East Automotive Tooling Molds Market Analysis By Material
Global Automotive Tooling & Molds Market, By Material Market Analysis (2024 - 2033)
The market by material indicates a clear dominance of metals, which represent around 64.8% market share in 2023, growing alongside the rising need for durable tooling solutions. Plastics, accounting for 27.08%, and composites at 8.12%, are also witnessing increased use with the rise of lightweight vehicle structures.
Asia Middle East Automotive Tooling Molds Market Analysis By Technology
Global Automotive Tooling & Molds Market, By Technology Market Analysis (2024 - 2033)
Injection molding dominates the technology segment, holding 64.8% of the market share in 2023. Blow molding and compression molding also retain significant shares; alongside advancements in additive manufacturing-driving the need for innovative tooling solutions.
Asia Middle East Automotive Tooling Molds Market Analysis By End Use
Global Automotive Tooling & Molds Market, By End Use Market Analysis (2024 - 2033)
The light vehicle segment is significantly large, with a market size of $2.46 billion in 2023, accounting for 64.8% of the total market. The heavy vehicles segment follows with a size of $1.03 billion and shares 27.08%, while electric vehicles are emerging with a notable presence.
Asia Middle East Automotive Tooling Molds Market Analysis By Application
Global Automotive Tooling & Molds Market, By Application Market Analysis (2024 - 2033)
Body parts applications lead with strong demand, representing 64.8% of the market share with a size of $2.46 billion. Interior and exterior parts are also crucial segments, indicating the broad applicability of tooling molds in vehicle manufacturing.
Asia Middle East Automotive Tooling Molds Market Analysis By Manufacturing Process
Global Automotive Tooling & Molds Market, By Manufacturing Process Market Analysis (2024 - 2033)
Additive manufacturing is gaining traction, accounting for 64.8% market share. This technology enables more complex designs and customized solutions for vehicle parts, highlighting the shift towards sophisticated production techniques.
Asia Middle East Automotive Tooling Molds Market Trends and Future Forecast
Request a custom research report for industry.
Global Market Leaders and Top Companies in Asia Middle East Automotive Tooling Molds Industry
Haas Automation, Inc.:
Haas Automation is a leading manufacturer of CNC machine tools, widely recognized for its innovation in machining technology and tooling solutions for the automotive sector.Mold-Masters Limited:
Mold-Masters is renowned for its advanced hot runner systems, which significantly enhance the reliability and efficiency of mold manufacturing in the automotive industry.BASF SE:
BASF is a global leader in chemicals and specializes in providing advanced polymer solutions for automotive tooling, contributing to increased efficiency in production.Alpine Engineering & Tooling, Inc.:
Alpine Engineering offers comprehensive tooling and engineering services for the automotive industry, focusing on precision and sustainability in production.We're grateful to work with incredible clients.
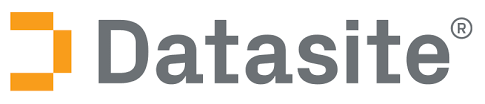
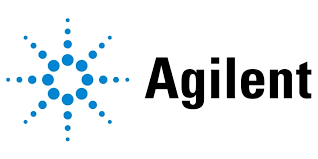

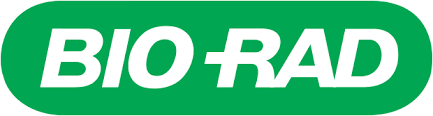
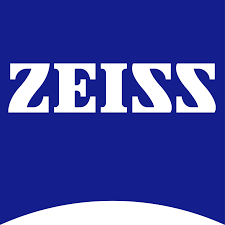
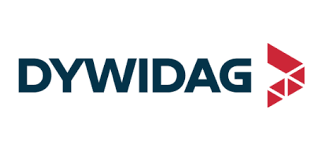
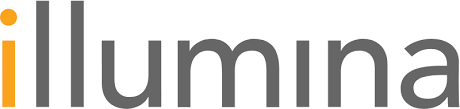

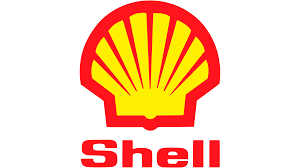
Related Industries
FAQs
What is the market size of Asia-Middle East Automotive Tooling Molds?
The Asia-Middle East Automotive Tooling Molds market is currently valued at approximately $3.8 billion, with a notable compound annual growth rate (CAGR) of 6.7%. This robust growth reflects the increasing demand for advanced automotive manufacturing techniques.
What are the key market players or companies in this industry?
The key players in the Asia-Middle East Automotive Tooling Molds industry include major manufacturers and suppliers specializing in various aspects of tooling and mold production, contributing significantly to innovation and market growth.
What are the primary factors driving the growth in the industry?
Key drivers for growth include the rapid expansion of the automotive sector, the increasing demand for electric vehicles, and advancements in molding technologies that improve production efficiency and quality.
Which region is the fastest Growing in the Automotive Tooling Molds market?
The Asia-Pacific region is currently the fastest-growing market, projected to increase from $0.70 billion in 2023 to $1.35 billion by 2033, driven by robust automotive production and expanding consumer demand.
Does Consainsights provide customized market report data for this industry?
Yes, Consainsights offers customized market report data tailored to specific needs, ensuring that clients receive detailed insights that are relevant to their business objectives and industry dynamics.
What deliverables can I expect from this market research project?
Deliverables include comprehensive market analysis, segmentation insights, competitive landscape data, and detailed regional analysis to inform strategic decision-making in the Automotive Tooling Molds industry.
What are the market trends of Automotive Tooling Molds?
Current trends include a shift towards sustainable materials, increased adoption of automation in manufacturing processes, and the growing use of 3D printing technologies in mold design and production.