Cnc Controller Market Size, Share, Industry Trends and Forecast to 2033
This report provides an in-depth analysis of the Cnc Controller market, focusing on market trends, size forecasts, and competitive landscape from 2023 to 2033. Insights pertain to segment performance, regional dynamics, and future growth predictions.
Metric | Value |
---|---|
Study Period | 2023 - 2033 |
2023 Market Size | $3.80 Billion |
CAGR (2023-2033) | 7.2% |
2033 Market Size | $7.77 Billion |
Top Companies | Fanuc Corporation, Siemens AG, Mitsubishi Electric Corporation, Haas Automation, Inc., KUKA AG |
Last Modified Date | Invalid Date |
Cnc Controller Market Report (2023 - 2033)
Cnc Controller Market Overview
What is the Market Size & CAGR of Cnc Controller market in 2023?
Cnc Controller Industry Analysis
Cnc Controller Market Segmentation and Scope
Request a custom research report for industry.
Cnc Controller Market Analysis Report by Region
Europe Cnc Controller Market Report:
The European market for Cnc Controllers is anticipated to expand from $1.03 billion in 2023 to $2.11 billion by 2033. The presence of established manufacturing sectors and a strong emphasis on automation and precision engineering are significant growth drivers.Asia Pacific Cnc Controller Market Report:
The Asia Pacific region is set to experience significant growth in the Cnc Controller market, increasing from $0.73 billion in 2023 to $1.50 billion by 2033. Key markets include China and India, where rapid industrialization and a push towards automation are driving demand for CNC technologies.North America Cnc Controller Market Report:
North America is one of the largest markets for Cnc Controllers, expected to grow from $1.40 billion in 2023 to $2.86 billion by 2033. The region is characterized by a strong focus on technological innovation and the high demand for precision machining in key industries.South America Cnc Controller Market Report:
In South America, the Cnc Controller market is projected to grow from $0.18 billion in 2023 to $0.38 billion by 2033. The region is gradually adopting advanced manufacturing processes, fueled by increasing investments in the industrial sector.Middle East & Africa Cnc Controller Market Report:
In the Middle East and Africa, the Cnc Controller market is projected to grow from $0.45 billion in 2023 to $0.93 billion by 2033. The region is witnessing increased investment in manufacturing capabilities, enhancing the demand for advanced Cnc Controllers.Request a custom research report for industry.
Cnc Controller Market Analysis By Type
Global CNC Controller Market, By Type Market Analysis (2024 - 2033)
The Cnc Controller market by type is primarily dominated by Open Loop Control Systems, which hold a market size of $2.38 billion in 2023 and are expected to grow to $4.86 billion by 2033, representing a market share of 62.56%. Closed Loop Control Systems follow with a market size of $0.91 billion in 2023, growing to $1.85 billion by 2033, capturing 23.88% of the market share. Hybrid Control Systems, although smaller, show significant growth potential with sizes projected at $0.52 billion in 2023 to $1.05 billion by 2033 (13.56% market share).
Cnc Controller Market Analysis By Technology
Global CNC Controller Market, By Technology Market Analysis (2024 - 2033)
In terms of technology, CNC Software constitutes a major segment, with a market size of $2.38 billion in 2023 and a projected increase to $4.86 billion by 2033, representing a robust presence of 62.56%. Hardware Controllers exhibit notable growth as well, moving from $0.91 billion in 2023 to $1.85 billion by 2033, maintaining a 23.88% market share. Emerging technologies are critical in driving innovation and operational efficiency across CNC systems.
Cnc Controller Market Analysis By Application
Global CNC Controller Market, By Application Market Analysis (2024 - 2033)
The application segmentation showcases Manufacturing as the largest contributor, growing from $2.02 billion in 2023 to $4.12 billion by 2033 (53.06% market share). Machining Services, although sized smaller, are also significantly growing from $0.86 billion in 2023 to $1.76 billion by 2033 (22.68% share). Other applications in Research and Development, Education, and niche sectors continue to contribute to overall growth.
Cnc Controller Market Analysis By End User
Global CNC Controller Market, By End-User Industry Market Analysis (2024 - 2033)
End-user analysis indicates Aerospace as a leading industry, valued at $2.02 billion in 2023 and anticipated to grow to $4.12 billion by 2033 (53.06% market share). Automotive and Medical industries follow with growth forecasts from $0.86 billion to $1.76 billion (22.68% share) and $0.51 billion to $1.05 billion (13.5% share) respectively. These sectors emphasize the need for precision and automation, driving demand for cutting-edge Cnc Controllers.
Cnc Controller Market Trends and Future Forecast
Request a custom research report for industry.
Global Market Leaders and Top Companies in Cnc Controller Industry
Fanuc Corporation:
A leading global provider of automation solutions, Fanuc Corporation specializes in robotics, CNC systems, and factory automation technologies.Siemens AG:
Siemens AG is a multinational conglomerate that plays a crucial role in manufacturing and automation technology, providing innovative CNC solutions.Mitsubishi Electric Corporation:
Known for its advanced automation technology, Mitsubishi Electric offers a wide range of CNC controllers and systems for various applications.Haas Automation, Inc.:
Haas Automation is one of the largest builders of CNC machine tools in America, providing robust and affordable CNC control solutions.KUKA AG:
KUKA AG is a key player in the automation industry, offering a variety of CNC systems for different sectors, including automotive and aerospace.We're grateful to work with incredible clients.
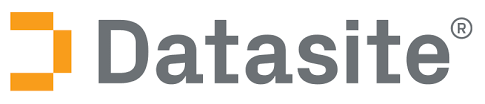
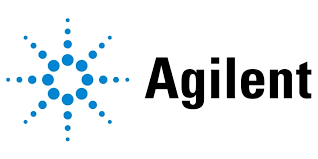

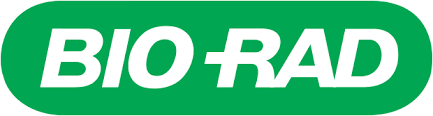
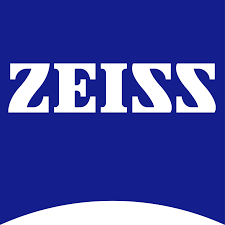
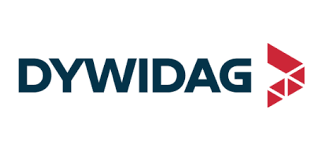
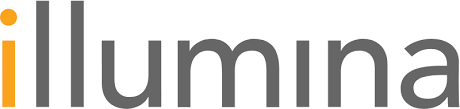

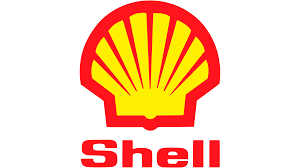
Related Industries
FAQs
What is the market size of CNC Controller?
The CNC Controller market is currently valued at $3.8 billion with a projected CAGR of 7.2% from 2023 to 2033. This growth indicates strong demand across various industries utilizing CNC technology for precision engineering and automation.
What are the key market players or companies in the CNC Controller industry?
Key players in the CNC Controller market include companies like Siemens AG, Fanuc Corporation, and Mitsubishi Electric, among others. These companies lead in technology innovation and hold significant market shares.
What are the primary factors driving the growth in the CNC Controller industry?
Factors driving CNC Controller market growth include increasing automation in manufacturing, demand for precision engineering, and advancements in software technology. The growing aerospace and automotive industries further enhance market potential.
Which region is the fastest Growing in the CNC Controller market?
The fastest-growing region in the CNC Controller market is Europe, projected to grow from $1.03 billion in 2023 to $2.11 billion by 2033, driven by robust industrial activities and increased investment in technology.
Does ConsaInsights provide customized market report data for the CNC Controller industry?
Yes, ConsaInsights offers customized market report data tailored to specific needs within the CNC Controller industry, allowing clients to gain insights relevant to their operations and strategic decisions.
What deliverables can I expect from this CNC Controller market research project?
Deliverables from the CNC Controller market research project include detailed market analysis reports, growth forecasts, competitive landscape assessments, and insights into regional market trends and segment performance.
What are the market trends of CNC Controller?
Current trends in the CNC Controller market include the rise of smart manufacturing, integration of IoT technologies, and the shift towards eco-friendly production methods, enhancing efficiency and reducing waste.