Coating Equipment Market Size, Share, Industry Trends and Forecast to 2033
This market report provides a comprehensive analysis of the Coating Equipment market, focusing on industry trends, market size, and growth forecast from 2023 to 2033. It covers segmentation, regional insights, and profiles of leading global players driving market advancements.
Metric | Value |
---|---|
Study Period | 2023 - 2033 |
2023 Market Size | $8.30 Billion |
CAGR (2023-2033) | 7.2% |
2033 Market Size | $16.97 Billion |
Top Companies | Graco Inc., Caterpillar Inc., Nordson Corporation, SAMES KREMLIN |
Last Modified Date | Invalid Date |
Coating Equipment Market Report (2023 - 2033)
Coating Equipment Market Overview
What is the Market Size & CAGR of Coating Equipment market in 2033?
Coating Equipment Industry Analysis
Coating Equipment Market Segmentation and Scope
Request a custom research report for industry.
Coating Equipment Market Analysis Report by Region
Europe Coating Equipment Market Report:
Europe's Coating Equipment market is set to grow from $2.37 billion in 2023 to $4.85 billion by 2033. This growth is influenced by stringent environmental regulations that prompt industries to invest in advanced coating technologies. The automotive and aerospace sectors are major end-users in this region, contributing significantly to market development.Asia Pacific Coating Equipment Market Report:
The Asia Pacific region represented a market size of approximately $1.56 billion in 2023, which is projected to grow to around $3.19 billion by 2033. This significant growth is driven by rapid industrialization and increasing manufacturing capabilities in countries like China and India. The demand for Coating Equipment, particularly in the automotive and construction sectors, is propelling market expansion across the region.North America Coating Equipment Market Report:
North America is one of the leading regions in the Coating Equipment market, with a market size of approximately $3.22 billion in 2023, expected to reach $6.58 billion by 2033. The US and Canada are significant contributors driven by technological innovations and a strong automotive industry. The focus on environmental regulations and sustainable products is also pushing manufacturers towards advanced coating technologies.South America Coating Equipment Market Report:
In South America, the Coating Equipment market is experiencing moderate growth, with sizes expected to increase from $0.51 billion in 2023 to $1.04 billion by 2033. Economic growth in Brazil and Argentina is expected to enhance infrastructural projects, thereby increasing demand for coatings. The government initiatives to boost manufacturing will further contribute to this market's development.Middle East & Africa Coating Equipment Market Report:
The Middle East and Africa region presents a growing opportunity in the Coating Equipment market, anticipated to grow from $0.63 billion in 2023 to $1.29 billion by 2033. The increase in manufacturing activities and infrastructural projects, particularly in the UAE and South Africa, boosts the demand for effective coating solutions.Request a custom research report for industry.
Coating Equipment Market Analysis By Coating Type
Global Coating Equipment Market, By Coating Type Market Analysis (2024 - 2033)
The market is predominantly driven by liquid coatings, which constituted about 67.91% of the market share in 2023. This segment's size is expected to grow from $5.64 billion to $11.52 billion by 2033. Spray coating also holds a significant position with a share of 56.02%, showing promising growth from $4.65 billion to $9.50 billion. Electrostatic and screen printing coatings, while smaller segments, are seeing increased adoption due to their efficiency and precision in application.
Coating Equipment Market Analysis By Application Industry
Global Coating Equipment Market, By Application Industry Market Analysis (2024 - 2033)
The automotive industry leads the application segments at a market share of 44% in 2023, expected to reach $7.47 billion by 2033. Following this, construction and electronics sectors show significant demand with shares of 24.67% and 10.67% respectively. These sectors are increasingly focusing on high-performance coatings to enhance product durability and aesthetic appeal, further driving the market growth.
Coating Equipment Market Analysis By Technology
Global Coating Equipment Market, By Technology Market Analysis (2024 - 2033)
Innovative technologies are reshaping the Coating Equipment landscape. Advancements in electrostatic coating technologies are enhancing application efficiency and reducing waste. Meanwhile, advancements in automation technology are streamlining production processes in various industries. Companies are increasingly investing in R&D to explore new materials and processes, making technology a pivotal component in the industry's growth.
Coating Equipment Market Analysis By End User
Global Coating Equipment Market, By End-User Market Analysis (2024 - 2033)
Manufacturers and contractors represent the leading end-users, holding a combined market share of over 77% in 2023. This sector is expected to grow significantly due to increasing industrial manufacturing activities and expanding construction projects globally. Research institutes and government agencies are gaining traction, emphasizing advancements in coating applications, thus contributing positively to the industry's overall growth.
Coating Equipment Market Trends and Future Forecast
Request a custom research report for industry.
Global Market Leaders and Top Companies in Coating Equipment Industry
Graco Inc.:
Graco Inc. is a leading manufacturer of fluid handling equipment, specializing in spray application systems for various industries. Their innovative technologies cater to the diverse needs of coating processes, providing superior performance and efficiency.Caterpillar Inc.:
Caterpillar Inc. produces a wide range of machinery and equipment, including advanced coating solutions designed for heavy-duty performance in construction and industrial applications, enhancing productivity and durability.Nordson Corporation:
Nordson Corporation is a global leader in precision dispensing equipment and advanced coating solutions. Their innovation in powder and liquid coating technologies helps industries achieve effective surface finishes.SAMES KREMLIN:
Known for their expertise in spray application technology, SAMES KREMLIN offers innovative solutions for both industrial and decorative coating applications, supporting various sectors including automotive and construction.We're grateful to work with incredible clients.
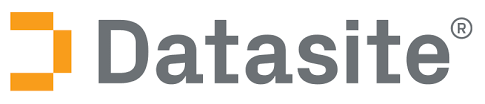
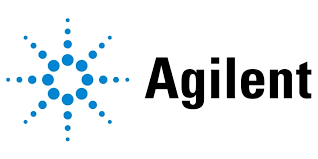

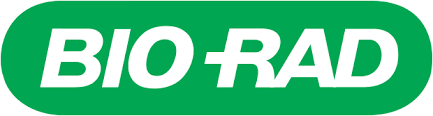
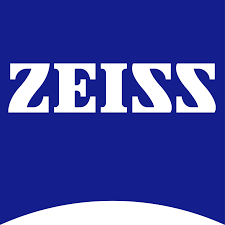
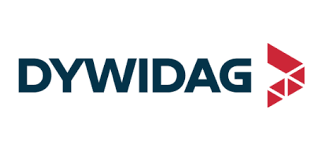
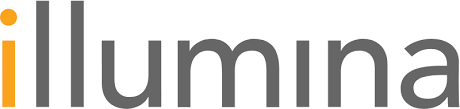

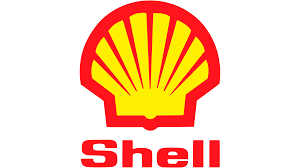
Related Industries
FAQs
What is the market size of coating equipment?
The global coating equipment market is valued at approximately $8.3 billion in 2023 and is projected to grow at a CAGR of 7.2%, potentially reaching significant market sizes by 2033.
What are the key market players or companies in the coating equipment industry?
The key players in the coating equipment market include some of the largest manufacturers, contractors, and research institutions, all contributing to the robust landscape of this industry, ensuring innovation and market expansion.
What are the primary factors driving the growth in the coating equipment industry?
Growing demand across sectors like automotive, electronics, and construction, along with technological advancements, are primary factors driving the growth in the coating equipment industry, pushing manufacturers to innovate continuously.
Which region is the fastest Growing in the coating equipment?
The Asia Pacific region is the fastest-growing market for coating equipment, expected to increase from $1.56 billion in 2023 to $3.19 billion by 2033, reflecting robust industrial growth and demand.
Does ConsaInsights provide customized market report data for the coating equipment industry?
Yes, ConsaInsights offers customized market research reports tailored to specific needs within the coating equipment industry, providing clients with precise and actionable insights tailored to their operational requirements.
What deliverables can I expect from this coating equipment market research project?
Expect comprehensive deliverables including detailed market analysis, growth forecasts, competitive landscape studies, and actionable insights into market trends which will inform strategic planning.
What are the market trends of coating equipment?
Current trends in the coating equipment market include a shift towards eco-friendly coatings, technological advancements in application methods, and increasing automation, reflecting an evolving landscape aligned with sustainability.