Composite Metal Finishing Market Size, Share, Industry Trends and Forecast to 2033
This report presents a comprehensive analysis of the Composite Metal Finishing market, including market dynamics, size forecasts, segmented insights, regional analyses, and trends expected from 2023 to 2033.
Metric | Value |
---|---|
Study Period | 2023 - 2033 |
2023 Market Size | $15.30 Billion |
CAGR (2023-2033) | 5.8% |
2033 Market Size | $27.25 Billion |
Top Companies | Alcoa Corporation, Parker Hannifin Corporation, Metal Finishing Technologies, Coventya International |
Last Modified Date | Invalid Date |
Composite Metal Finishing Market Report (2023 - 2033)
Composite Metal Finishing Market Overview
What is the Market Size & CAGR of Composite Metal Finishing market in 2023?
Composite Metal Finishing Industry Analysis
Composite Metal Finishing Market Segmentation and Scope
Request a custom research report for industry.
Composite Metal Finishing Market Analysis Report by Region
Europe Composite Metal Finishing Market Report:
The European market is valued at $4.33 billion in 2023 and is projected to grow to $7.71 billion by 2033, led by stringent regulations promoting sustainability and quality in manufacturing processes.Asia Pacific Composite Metal Finishing Market Report:
In 2023, the Asia Pacific region is valued at $2.98 billion, projected to grow to $5.31 billion by 2033. This growth is driven by rapid industrialization, an expanding automotive sector, and rising consumer electronics production.North America Composite Metal Finishing Market Report:
North America holds a significant share, with a market value of $5.60 billion in 2023, projected to increase to $9.97 billion by 2033. The robust aerospace and automotive industries in this region are major contributors to market expansion.South America Composite Metal Finishing Market Report:
The South American market, valued at $1.02 billion in 2023, is expected to reach $1.82 billion by 2033. The growth is fueled by increasing demand for metal finishing in mining and construction industries.Middle East & Africa Composite Metal Finishing Market Report:
The Middle East and Africa market is anticipated to grow from $1.37 billion in 2023 to $2.44 billion by 2033. Growth factors include investment in infrastructure and manufacturing capabilities.Request a custom research report for industry.
Composite Metal Finishing Market Analysis By Production Process
Global Composite Metal Finishing Market, By Production Process Market Analysis (2024 - 2033)
The production process segment of Composite Metal Finishing includes methods such as electroplating, anodizing, and electroless plating. In 2023, electroplating dominates the market with a size of $9.54 billion and a market share of 62.37%. Anodizing follows with a revenue of $2.46 billion, accounting for 16.1%. As manufacturing processes evolve, innovations in these techniques are anticipated to drive growth, particularly in automotive and aerospace applications.
Composite Metal Finishing Market Analysis By Material
Global Composite Metal Finishing Market, By Material Market Analysis (2024 - 2033)
Aluminum leads the material segment with a market size of $8.01 billion in 2023, holding a significant share of 52.34%. Zinc materials follow at $3.73 billion with a 24.36% share, while copper is valued at $1.83 billion. The demand for aluminum in automotive and consumer goods applications fuels this segment's growth, supported by its lightweight and corrosion resistance properties.
Composite Metal Finishing Market Analysis By Application
Global Composite Metal Finishing Market, By Application Market Analysis (2024 - 2033)
The automotive sector represents the largest application segment in the Composite Metal Finishing market, valued at $6.81 billion in 2023, which constitutes 44.49% of the market. Aerospace and electronics also contribute significantly, valued at $3.46 billion and $1.61 billion respectively. Increasing vehicle production and the demand for lightweight materials propel growth in automotive applications.
Composite Metal Finishing Market Analysis By Finish Type
Global Composite Metal Finishing Market, By Finish Type Market Analysis (2024 - 2033)
Among finish types, matte finishing leads with a size of $8.01 billion, comprising 52.34% of the market in 2023. Glossy and specialized finishes also show substantial demand, reported at $3.73 billion and $1.74 billion respectively. Consumer preferences for aesthetics coupled with advances in finishing technologies are key drivers of this segment.
Composite Metal Finishing Market Trends and Future Forecast
Request a custom research report for industry.
Global Market Leaders and Top Companies in Composite Metal Finishing Industry
Alcoa Corporation:
Alcoa is a leading player in the aluminum industry, contributing significantly to the Composite Metal Finishing sector through its high-performance aluminum products and innovative finishing solutions.Parker Hannifin Corporation:
Parker Hannifin specializes in motion and control technologies and offers advanced metal finishing solutions utilized in numerous applications, particularly in aerospace.Metal Finishing Technologies:
A pioneer in the field of electroplating, Metal Finishing Technologies provides a variety of seamless and custom finishing solutions for industrial applications.Coventya International:
Coventya is known for its innovative and environmentally friendly finishing products, widely adopted in automotive and electronics manufacturing.We're grateful to work with incredible clients.
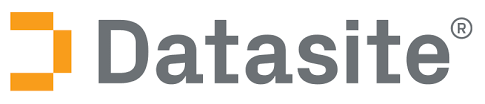
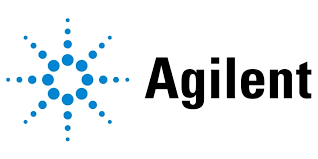

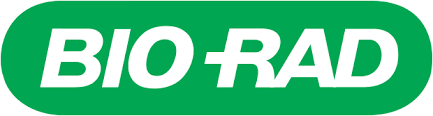
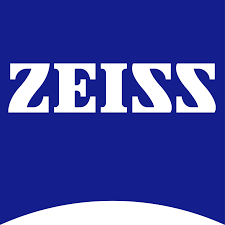
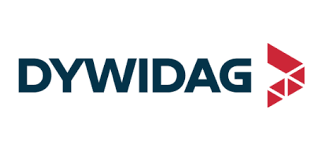
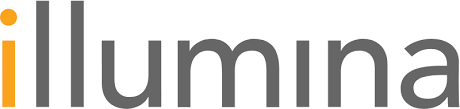

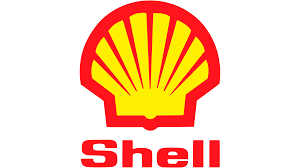
Related Industries
FAQs
What is the market size of composite Metal Finishing?
The composite metal finishing market is currently valued at approximately $15.3 billion in 2023, with a projected CAGR of 5.8% from 2023 to 2033, indicating substantial growth opportunities in the industry over the next decade.
What are the key market players or companies in this composite Metal Finishing industry?
Key players in the composite metal finishing industry include prominent companies such as Atotech, Huntsman Corporation, and Coventya, all of which offer a range of solutions catering to metal finishing applications across various sectors, enhancing competitiveness.
What are the primary factors driving the growth in the composite Metal Finishing industry?
Growth in the composite metal finishing industry is primarily driven by the increasing demand from the automotive and aerospace sectors, rising industrialization, technological advancements in finishing processes, and the growing emphasis on aesthetic and corrosion resistance in various applications.
Which region is the fastest Growing in the composite Metal Finishing?
The fastest-growing region in the composite metal finishing market is Asia Pacific, where market size is expected to grow from $2.98 billion in 2023 to $5.31 billion in 2033, reflecting a robust demand surge in manufacturing and electronics in the region.
Does ConsaInsights provide customized market report data for the composite Metal Finishing industry?
Yes, ConsaInsights offers customized market report data tailored to specific needs within the composite metal finishing industry, ensuring clients receive relevant insights and detailed analyses that align with their strategic goals.
What deliverables can I expect from this composite Metal Finishing market research project?
Expect deliverables including detailed market analysis reports, competitive landscape assessments, regional market evaluations, segment-wise insights, trends analyses, and forecasts, all packaged for informed decision-making in the composite metal finishing industry.
What are the market trends of composite Metal Finishing?
Current market trends in composite metal finishing include a shift towards eco-friendly processes, increasing adoption of automation, and growing demand for advanced materials. The sector is also experiencing innovation in surface finishing techniques to meet evolving customer requirements.