Composite Tooling Market Size, Share, Industry Trends and Forecast to 2033
This report provides a comprehensive analysis of the Composite Tooling market, focusing on key insights, trends, and forecasts from 2023 to 2033. It covers market size, CAGR, segmentations, regional insights, and industry dynamics essential for stakeholders.
Metric | Value |
---|---|
Study Period | 2023 - 2033 |
2023 Market Size | $2.50 Billion |
CAGR (2023-2033) | 6.8% |
2033 Market Size | $4.91 Billion |
Top Companies | Hexcel Corporation, Toray Industries, Inc., Mitsubishi Chemical Corporation, SGL Carbon SE, Safran |
Last Modified Date | Invalid Date |
Composite Tooling Market Report (2023 - 2033)
Composite Tooling Market Overview
What is the Market Size & CAGR of Composite Tooling market in 2023?
Composite Tooling Industry Analysis
Composite Tooling Market Segmentation and Scope
Request a custom research report for industry.
Composite Tooling Market Analysis Report by Region
Europe Composite Tooling Market Report:
Europe's Composite Tooling market is expected to grow from $0.68 billion in 2023 to $1.33 billion by 2033. The stringent regulations regarding emissions and energy efficiency are driving demand in the automotive and aerospace sectors, pushing manufacturers towards lightweight composite tooling solutions to meet these standards.Asia Pacific Composite Tooling Market Report:
In the Asia Pacific region, the Composite Tooling market is expected to grow from $0.47 billion in 2023 to $0.93 billion by 2033. The growth is propelled by the increasing manufacturing activities and investments in aerospace and automotive industries. Countries like China and Japan are at the forefront, adopting advanced materials and technologies, thus significantly contributing to the market's expansion.North America Composite Tooling Market Report:
North America stands as one of the largest markets for Composite Tooling, anticipated to reach $1.91 billion by 2033 from $0.97 billion in 2023. The aerospace and automotive sectors are significant contributors, supported by technological advancements and a robust supply chain. Companies are focusing more on sustainable practices, enhancing the demand for innovative composite solutions.South America Composite Tooling Market Report:
South America is projected to grow from $0.21 billion in 2023 to $0.41 billion by 2033. Economic growth in Brazil and Argentina, coupled with efforts to enhance infrastructure, will drive demand for composite tooling, especially in the construction sector, as manufacturers look to innovative materials to improve product offerings.Middle East & Africa Composite Tooling Market Report:
The Middle East and Africa region is projected to expand from $0.16 billion in 2023 to $0.32 billion by 2033. With burgeoning investments in wind energy and infrastructure, there is a growing need for composite tooling, particularly in the renewable energy segment, thereby contributing to the market growth.Request a custom research report for industry.
Composite Tooling Market Analysis By Product
Global Composite Tooling Market, By Product Market Analysis (2024 - 2033)
The key products within the Composite Tooling market include Hand Layup, Vacuum Infusion, and Filament Winding. In 2023, the Hand Layup segment leads with a market size of $1.42 billion and is expected to increase to $2.78 billion by 2033. Vacuum Infusion is also a significant contributor, with a market size projected to grow from $0.61 billion to $1.20 billion in the same timeframe.
Composite Tooling Market Analysis By Application
Global Composite Tooling Market, By Application Market Analysis (2024 - 2033)
The major applications in the Composite Tooling market include Aerospace, Automotive, Industrial Manufacturing, and Wind Energy. The Aerospace segment, valued at $1.02 billion in 2023, is likely to reach $2.01 billion by 2033. Similarly, the Automotive segment will grow from $0.59 billion to $1.16 billion, reflecting the increasing adoption of lightweight materials.
Composite Tooling Market Analysis By End User
Global Composite Tooling Market, By End-User Industry Market Analysis (2024 - 2033)
End-user industries for composite tooling encompass Aerospace, Automotive, Marine, and Sports & Recreation. Aerospace accounts for a substantial share (around 40.84%) in 2023, reflecting its crucial role in driving demands for lightweight tooling solutions.
Composite Tooling Market Analysis By Material Type
Global Composite Tooling Market, By Material Type Market Analysis (2024 - 2033)
Material types in the Composite Tooling market include Thermosets, Thermoplastics, and Resins. Thermosets lead with a market share of 56.66% in 2023 and are expected to maintain a strong position due to their superior mechanical properties, while Thermoplastics are projected to capture 24.52% of the market share.
Composite Tooling Market Analysis By Process
Global Composite Tooling Market, By Manufacturing Process Market Analysis (2024 - 2033)
The manufacturing processes for Composite Tooling include Hand Layup and Vacuum Infusion, with Hand Layup being the most prominent method used due to its simplicity and low cost. The industry trend indicates a shift towards advanced automated processes, enhancing efficiency and product precision.
Composite Tooling Market Trends and Future Forecast
Request a custom research report for industry.
Global Market Leaders and Top Companies in Composite Tooling Industry
Hexcel Corporation:
A leading global provider of advanced composite materials, Hexcel Corporation plays a significant role in the aerospace and automotive sectors, focusing on innovation and sustainability.Toray Industries, Inc.:
A prominent player in the Composite Tooling market, Toray is recognized for its extensive research in carbon fiber composites and high-performance materials, catering to diverse industries.Mitsubishi Chemical Corporation:
Mitsubishi Chemical is heavily involved in producing composite materials and tooling solutions, supporting automation and advanced manufacturing technologies across various sectors.SGL Carbon SE:
As a key supplier of carbon fiber and composite materials, SGL Carbon is instrumental in expanding the applications of composites in automotive, aerospace, and other high-performance sectors.Safran:
Safran specializes in aerospace component manufacturing and engineering essential tools and materials that enhance performance and efficiency in the aerospace sector.We're grateful to work with incredible clients.
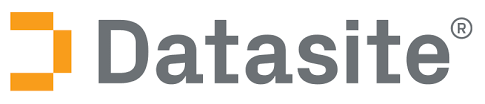
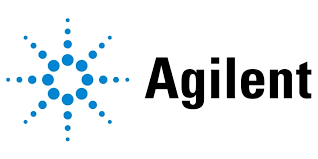

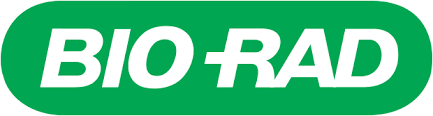
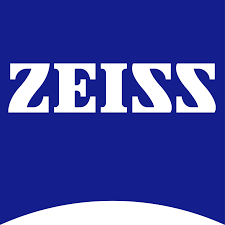
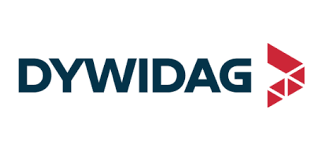
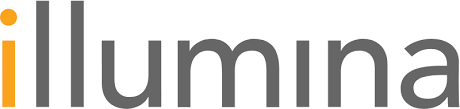

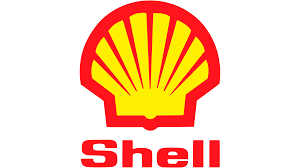
Related Industries
FAQs
What is the market size of composite Tooling?
The composite tooling market is currently valued at approximately $2.5 billion in 2023, and it is projected to grow at a CAGR of 6.8%, indicating robust expansion and increasing adoption of composite materials in various industries.
What are the key market players or companies in the composite Tooling industry?
Key players in the composite tooling industry include global manufacturing leaders and material suppliers. Notable companies often focus on advanced manufacturing technologies, ensuring innovation in tooling solutions and meeting the growing demand within aerospace, automotive, and construction sectors.
What are the primary factors driving the growth in the composite Tooling industry?
The growth of the composite tooling industry is driven by factors such as increasing demand for lightweight materials in automotive and aerospace applications, advancements in manufacturing technologies, and a growing emphasis on sustainability and energy efficiency in production processes.
Which region is the fastest Growing in the composite Tooling?
Asia Pacific is currently one of the fastest-growing regions in the composite tooling market, projected to grow from $0.47 billion in 2023 to $0.93 billion by 2033, driven by rising industrialization and demand for advanced materials in manufacturing.
Does ConsaInsights provide customized market report data for the composite Tooling industry?
Yes, ConsaInsights offers customized market report data tailored to specific needs in the composite tooling industry, enabling clients to gain insights based on unique criteria, target markets, and focus areas for informed decision-making.
What deliverables can I expect from this composite Tooling market research project?
Clients can expect comprehensive deliverables including detailed market analysis, growth forecasts, competitive landscape assessments, regional insights, and segment-wise breakdowns of the composite tooling market to inform strategic planning.
What are the market trends of composite Tooling?
Current market trends in composite tooling include increasing adoption of automation technologies, a shift towards eco-friendly materials, and heightened research and development efforts aimed at enhancing tooling efficiency and product performance across industries.