Computer Numerical Controls Cnc Market Size, Share, Industry Trends and Forecast to 2033
This report provides an in-depth analysis of the Computer Numerical Controls (CNC) market from 2023 to 2033, offering insights into market size, growth forecasts, technologies, regional dynamics, key players, and emerging trends.
Metric | Value |
---|---|
Study Period | 2023 - 2033 |
2023 Market Size | $75.60 Billion |
CAGR (2023-2033) | 6.8% |
2033 Market Size | $148.59 Billion |
Top Companies | Haas Automation, FANUC Corporation, Siemens AG, Emco GmbH, Okuma Corporation |
Last Modified Date | Invalid Date |
Computer Numerical Controls Cnc Market Report (2023 - 2033)
Computer Numerical Controls Cnc Market Overview
What is the Market Size & CAGR of Computer Numerical Controls Cnc market in 2023?
Computer Numerical Controls Cnc Industry Analysis
Computer Numerical Controls Cnc Market Segmentation and Scope
Request a custom research report for industry.
Computer Numerical Controls Cnc Market Analysis Report by Region
Europe Computer Numerical Controls Cnc Market Report:
The European CNC market is estimated to grow from $25.54 billion in 2023 to $50.19 billion by 2033, upheld by stringent quality standards and a strong automotive and aerospace industry, fostering a continuous demand for precision tooling.Asia Pacific Computer Numerical Controls Cnc Market Report:
In the Asia Pacific region, the CNC market is anticipated to grow from $13.56 billion in 2023 to $26.64 billion in 2033, driven by rapid industrialization, particularly in countries like China and India. Increased investment in automation and machinery upgrades across manufacturing sectors is fueling market growth.North America Computer Numerical Controls Cnc Market Report:
North America is projected to be the largest market, growing from $27.16 billion in 2023 to $53.39 billion by 2033. The presence of established manufacturing sectors and a strong focus on technological integration are significant growth drivers in this region.South America Computer Numerical Controls Cnc Market Report:
South America is expected to see moderate growth in the CNC market, expanding from $4.78 billion in 2023 to $9.39 billion by 2033. Factors such as advancements in manufacturing capabilities and increased exports in various segments will contribute to this growth.Middle East & Africa Computer Numerical Controls Cnc Market Report:
The Middle East and Africa region are predicted to witness growth from $4.57 billion in 2023 to $8.97 billion in 2033, with increasing investments in infrastructure and manufacturing technologies enhancing CNC adoption.Request a custom research report for industry.
Computer Numerical Controls Cnc Market Analysis By Product Type
Global CNC Market, By Product Type Market Analysis (2024 - 2033)
The CNC market by product type is dominated by CNC machines, forecasted to grow from $49.83 billion in 2023 to $97.93 billion in 2033, representing a robust CAGR. CNC software and accessories also play a vital role, with sizes growing from $21.41 billion to $42.08 billion and $4.36 billion to $8.57 billion, respectively, highlighting the importance of support technology in CNC operations.
Computer Numerical Controls Cnc Market Analysis By Technology
Global CNC Market, By Technology Market Analysis (2024 - 2033)
The 2D CNC technology plays a leading role, accounting for a major share of the market, with projections of growth from $49.83 billion in 2023 to $97.93 billion in 2033. Meanwhile, 3D CNC technology and micro CNC technology are expected to increase from $21.41 billion to $42.08 billion and $4.36 billion to $8.57 billion, showcasing significant advancements in complexity and precision.
Computer Numerical Controls Cnc Market Analysis By Application
Global CNC Market, By Application Market Analysis (2024 - 2033)
In application segmentation, the aerospace and defense sector accounts for the largest share, expected to grow from $31.15 billion in 2023 to $61.22 billion in 2033. Other sectors like automotive and electronics offer substantial opportunities, with market sizes increasing from $15.48 billion and $11.24 billion, respectively, emphasizing the ubiquitous need for CNC solutions across industries.
Computer Numerical Controls Cnc Market Analysis By End User
Global CNC Market, By End-User Industry Market Analysis (2024 - 2033)
CNC technology's applicability spans multiple end-user industries. In medical applications, growth from $7.66 billion to $15.05 billion is anticipated due to increased demand for precision instruments. The furniture sector will also see an increase from $10.08 billion to $19.81 billion, highlighting the versatility of CNC usage.
Computer Numerical Controls Cnc Market Trends and Future Forecast
Request a custom research report for industry.
Global Market Leaders and Top Companies in Computer Numerical Controls Cnc Industry
Haas Automation:
Haas Automation is a major player specializing in the manufacture of CNC machines and cutting tools. Its commitment to high-performance and durable products makes it a preferred choice in various industries.FANUC Corporation:
FANUC is a leading Japanese firm known for its automation products and CNC systems. Its pioneering technologies and smart factory solutions have significantly impacted manufacturing efficiency.Siemens AG:
Siemens AG provides a wide range of CNC and automation solutions, focusing on smart manufacturing and digitalization, making it a key player in driving technological innovation in the CNC market.Emco GmbH:
Emco offers a diverse range of CNC machines and is recognized for its educational and training systems that equip new generations of engineers with essential CNC skills.Okuma Corporation:
Okuma manufactures various CNC machines and is noted for its focus on precision tooling and energy-efficient products, catering to a wide array of manufacturing needs.We're grateful to work with incredible clients.
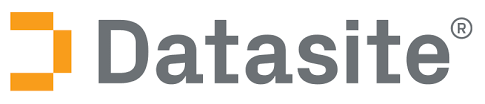
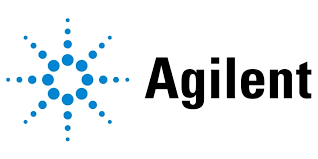

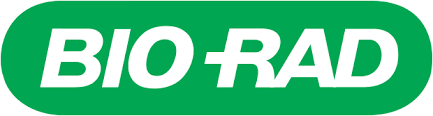
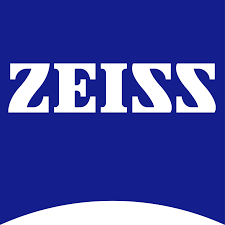
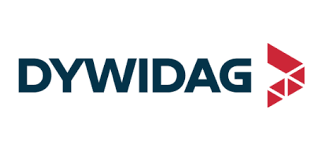
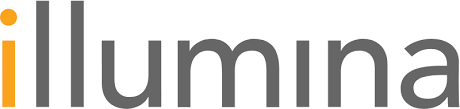

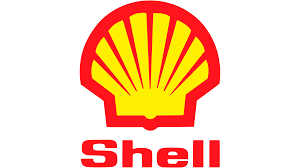
Related Industries
FAQs
What is the market size of Computer Numerical Controls (CNC)?
The global computer numerical controls (CNC) market is projected to reach a size of approximately $75.6 billion by 2033, with a compound annual growth rate (CAGR) of 6.8% from 2023 to 2033.
What are the key market players or companies in the CNC industry?
Key market players in the CNC industry include industry leaders like Siemens AG, FANUC Corporation, Haas Automation, Mitsubishi Electric Corporation, and DMG MORI. These companies dominate with innovative technologies and extensive market reach.
What are the primary factors driving the growth in the CNC industry?
Growth in the CNC industry is driven by increasing automation in manufacturing, advancements in technology, rising demand for precision machining, and the growing aerospace and automotive sectors that enhance the demand for CNC solutions.
Which region is the fastest Growing in the CNC market?
The Asia Pacific region is the fastest-growing market for CNC technologies, with an expected increase in market size from $13.56 billion in 2023 to $26.64 billion by 2033, fueled by industrial growth in nations like China and India.
Does ConsaInsights provide customized market report data for the CNC industry?
Yes, ConsaInsights offers customized market report data tailored to specific requirements of the CNC industry, ensuring that clients receive relevant and actionable insights based on their unique business needs.
What deliverables can I expect from this CNC market research project?
Deliverables include comprehensive market analysis reports, regional segment insights, competitive landscape evaluations, trend analysis, and projections for a variety of CNC technology applications over the next decade.
What are the market trends of Computer Numerical Controls (CNC)?
Current trends in the CNC market include an increased focus on automation and smart manufacturing, rising adoption of IoT-enabled machinery, and growth in hybrid CNC technologies, enhancing production efficiency and reducing operational costs.