Digital Manufacturing Software Market Size, Share, Industry Trends and Forecast to 2033
This report provides a comprehensive analysis of the Digital Manufacturing Software market from 2023 to 2033, including insights on market size, growth rates, regional dynamics, industry trends, and competitive landscape.
Metric | Value |
---|---|
Study Period | 2023 - 2033 |
2023 Market Size | $10.50 Billion |
CAGR (2023-2033) | 7.2% |
2033 Market Size | $21.46 Billion |
Top Companies | Siemens AG, Dassault Systèmes, PTC Inc., Autodesk, Inc. |
Last Modified Date | Invalid Date |
Digital Manufacturing Software Market Report (2023 - 2033)
Digital Manufacturing Software Market Overview
What is the Market Size & CAGR of Digital Manufacturing Software market in 2023?
Digital Manufacturing Software Industry Analysis
Digital Manufacturing Software Market Segmentation and Scope
Request a custom research report for industry.
Digital Manufacturing Software Market Analysis Report by Region
Europe Digital Manufacturing Software Market Report:
Europe, valued at $3.18 billion in 2023, is projected to expand to $6.49 billion by 2033. The emphasis on sustainability, alongside regulatory compliance in manufacturing processes, drives demand for digital manufacturing solutions across the automotive and aerospace sectors.Asia Pacific Digital Manufacturing Software Market Report:
The Asia-Pacific region, with a market size of $2.08 billion in 2023, is anticipated to grow to $4.26 billion by 2033. Driven by rapid industrialization and increasing adoption of smart manufacturing technologies, countries like China and India are pivotal in this growth trajectory. Government initiatives favoring digital transformation further support the market expansion.North America Digital Manufacturing Software Market Report:
North America is expected to dominate the market, with a size of $3.62 billion in 2023, scaling to $7.41 billion by 2033. The United States leads this growth, driven by technology innovation, advanced infrastructure, and the presence of key players focusing on integrating advanced manufacturing technologies.South America Digital Manufacturing Software Market Report:
In South America, the market size is projected at $1.03 billion for 2023, increasing to $2.10 billion by 2033. The region focuses on improving production efficiency in sectors such as automotive and consumer electronics, fostering technological advancements and partnerships with global software providers.Middle East & Africa Digital Manufacturing Software Market Report:
The Middle East and Africa exhibit a nascent market size of $0.59 billion in 2023, expected to grow to $1.21 billion by 2033. Increasing investment in infrastructure and technology, alongside growing manufacturing activities, propel market growth in this region.Request a custom research report for industry.
Digital Manufacturing Software Market Analysis By Software Type
Global Digital Manufacturing Software Market, By Software Type Market Analysis (2024 - 2033)
In 2023, the Integrated Solutions segment dominates with a market size of $7.16 billion, anticipated to reach $14.63 billion by 2033, maintaining a market share of 68.17%. Analytics and Reporting software follows with $2.96 billion in 2023, expected to grow to $6.04 billion. Automation Capabilities, while smaller, represents a vital growth area as businesses seek to enhance efficiency through automation.
Digital Manufacturing Software Market Analysis By Industry Application
Global Digital Manufacturing Software Market, By Industry Application Market Analysis (2024 - 2033)
The Automotive Industry Applications segment stands strong with a market size of $7.16 billion in 2023, projected to double by 2033. Aerospace Industry Applications are scaling as well, from $2.96 billion to $6.04 billion, showing the increasing reliance on digital manufacturing solutions in high-stakes industries. Moreover, the electronics sector also sees growth through tailored software designed to maximize precision and automation.
Digital Manufacturing Software Market Analysis By Deployment Type
Global Digital Manufacturing Software Market, By Deployment Type Market Analysis (2024 - 2033)
On-Premises Deployment will continue to lead the segment, valued at $9.02 billion in 2023 expected to rise to $18.45 billion. Conversely, Cloud-Based Deployment is also gaining traction, from $1.48 billion to $3.02 billion, offering flexibility and scalability that meets modern manufacturing needs.
Digital Manufacturing Software Market Analysis By Business Size
Global Digital Manufacturing Software Market, By Business Size Market Analysis (2024 - 2033)
The SME segment presents a lucrative market, leading with $9.02 billion in 2023 and forecasted to grow to $18.45 billion, showcasing the increasing digitalization of smaller manufacturers. In contrast, Large Enterprises, though smaller in size, exhibit robust expansion from $1.48 billion to $3.02 billion as they embrace comprehensive digital manufacturing solutions.
Digital Manufacturing Software Market Analysis By Feature
Global Digital Manufacturing Software Market, By Key Features Market Analysis (2024 - 2033)
Key features of digital manufacturing solutions span from product lifecycle management to advanced analytics capabilities. Solutions tailored with these features are essential as manufacturers focus on reliability and real-time data utilization to enhance production efficiency and quality control, ultimately driving significant market growth.
Digital Manufacturing Software Market Trends and Future Forecast
Request a custom research report for industry.
Global Market Leaders and Top Companies in Digital Manufacturing Software Industry
Siemens AG:
Siemens AG provides comprehensive digital solutions for manufacturing, focusing on automation, digitalization, and advanced simulation capabilities, leading the shift towards smart manufacturing.Dassault Systèmes:
Known for its 3D design software, Dassault Systèmes offers solutions that enhance product lifecycle management, enabling manufacturers to innovate and collaborate effectively.PTC Inc.:
PTC Inc. specializes in IoT and augmented reality solutions for manufacturing, enriching innovation through data-driven insights and enhancing efficiency across operations.Autodesk, Inc.:
Autodesk focuses on computer-aided design solutions, bringing advanced modeling tools that empower manufacturers in various sectors, notably in construction and engineering fields.We're grateful to work with incredible clients.
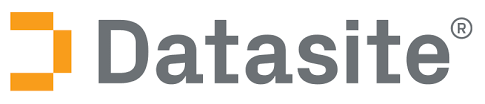
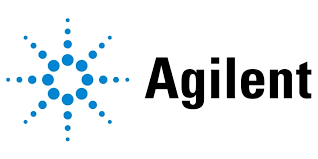

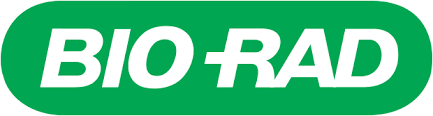
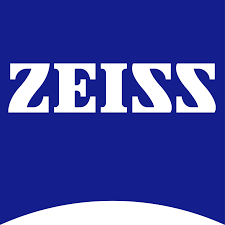
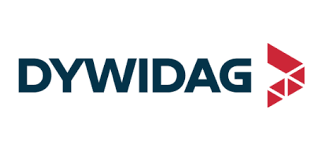
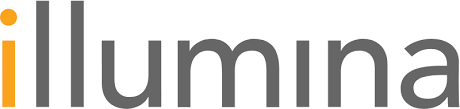

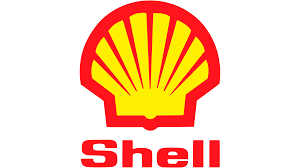
Related Industries
FAQs
What is the market size of digital Manufacturing Software?
The digital manufacturing software market is valued at approximately $10.5 billion in 2023 and is projected to grow at a CAGR of 7.2% through 2033. This growth reflects rising digitalization trends within the manufacturing sector.
What are the key market players or companies in the digital Manufacturing Software industry?
Key players in the digital manufacturing software industry include Siemens, Dassault Systems, PTC Inc., Autodesk, and Microsoft. These companies drive innovation and competitiveness through advanced digital solutions in manufacturing.
What are the primary factors driving the growth in the digital Manufacturing Software industry?
Growth in the digital manufacturing software industry is driven by the increasing adoption of Industry 4.0, demand for efficiency in manufacturing processes, and integration of advanced technologies like IoT and AI for smarter production systems.
Which region is the fastest Growing in the digital Manufacturing Software?
The fastest-growing region in the digital manufacturing software market is North America, with potential growth from $3.62 billion in 2023 to $7.41 billion by 2033, indicating strong demand for digital solutions in manufacturing.
Does ConsaInsights provide customized market report data for the digital Manufacturing Software industry?
Yes, ConsaInsights offers customized market report data for the digital manufacturing software industry, allowing clients to tailor insights to their specific needs and focus areas within the industry.
What deliverables can I expect from this digital Manufacturing Software market research project?
From the digital manufacturing software market research project, you can expect comprehensive reports including market size, growth forecasts, competitive analysis, and insights on key trends and technologies affecting the industry.
What are the market trends of digital Manufacturing Software?
Key market trends in digital manufacturing software include rising integration of AI and analytics, shift towards cloud-based solutions, increased emphasis on sustainability, and a growing focus on automating manufacturing processes to enhance productivity.