Fill Finish Manufacturing Market Size, Share, Industry Trends and Forecast to 2033
This report provides an in-depth analysis of the Fill Finish Manufacturing market, focusing on current conditions, industry trends, and forecasts for the period 2023-2033. Key insights on market size, segmentation, and regional dynamics are included, aiming to guide stakeholders in strategic decision-making.
Metric | Value |
---|---|
Study Period | 2023 - 2033 |
2023 Market Size | $12.00 Billion |
CAGR (2023-2033) | 9.5% |
2033 Market Size | $30.69 Billion |
Top Companies | Sartorius AG, Boehringer Ingelheim, West Pharmaceutical Services, Parexel International, Thermo Fisher Scientific |
Last Modified Date | Invalid Date |
Fill Finish Manufacturing Market Report (2023 - 2033)
Fill Finish Manufacturing Market Overview
What is the Market Size & CAGR of Fill Finish Manufacturing market in 2023?
Fill Finish Manufacturing Industry Analysis
Fill Finish Manufacturing Market Segmentation and Scope
Request a custom research report for industry.
Fill Finish Manufacturing Market Analysis Report by Region
Europe Fill Finish Manufacturing Market Report:
The European market is projected to grow from $4.07 billion in 2023 to $10.40 billion by 2033. Increasing regulations around drug safety and quality, coupled with a strong emphasis on biologics, are significant drivers, alongside ongoing investments in manufacturing technologies and infrastructure.Asia Pacific Fill Finish Manufacturing Market Report:
In 2023, the Fill Finish Manufacturing market in the Asia Pacific is valued at approximately $2.19 billion, with projections suggesting growth to $5.59 billion by 2033. The region benefits from a growing biopharmaceutical sector, increased investment in healthcare infrastructure, and favorable government policies promoting local manufacturing initiatives.North America Fill Finish Manufacturing Market Report:
North America continues to dominate the global Fill Finish Manufacturing market, with a size of $4.01 billion in 2023, anticipated to rise to $10.25 billion by 2033. The region is characterized by robust R&D activities, high healthcare expenditure, and a mature pharmaceutical landscape, making it a key player in technological advancements and production capabilities.South America Fill Finish Manufacturing Market Report:
South America is expected to see gradual growth in the Fill Finish Manufacturing sector, expanding from $0.31 billion in 2023 to $0.79 billion by 2033. This growth is driven by an increase in regional demand for pharmaceuticals and a shift towards outsourcing production to comply with international regulatory standards.Middle East & Africa Fill Finish Manufacturing Market Report:
Currently valued at $1.43 billion in 2023, the Fill Finish Manufacturing market in the Middle East and Africa is expected to grow to $3.66 billion by 2033. The region's growth is supported by rising healthcare expenditures and efforts to enhance local production capabilities, especially in countries like South Africa and the UAE.Request a custom research report for industry.
Fill Finish Manufacturing Market Analysis By Product
Global Fill-Finish Manufacturing Market, By Product Market Analysis (2024 - 2033)
The Fill Finish Manufacturing market segmentation by product shows significant growth across various categories. Liquid fillers encompass a massive market, expected to grow from $7.67 billion in 2023 to $19.61 billion in 2033, maintaining a market share of 63.88%. Semi-solid fillers are projected to rise from $2.44 billion to $6.23 billion, representing a 20.3% share. Solid fillers, although smaller, are also expected to expand from $1.90 billion to $4.86 billion, capturing 15.82% of the market.
Fill Finish Manufacturing Market Analysis By Technology
Global Fill-Finish Manufacturing Market, By Technology Market Analysis (2024 - 2033)
This segment features critical technologies like aseptic processing, which accounts for a market size forecasted to grow from $10.35 billion in 2023 to $26.48 billion by 2033, dominating with an 86.26% share. Terminal sterilization technologies, while smaller, will grow from $1.65 billion to $4.22 billion, holding a 13.74% market share. The advancement of these technologies signifies a focus on maintaining product sterility and safety.
Fill Finish Manufacturing Market Analysis By End User
Global Fill-Finish Manufacturing Market, By End-User Market Analysis (2024 - 2033)
The end-user segmentation reflects diversification in the Fill Finish Manufacturing market. Pharmaceutical companies lead with a substantial market size of $7.67 billion expected to reach $19.61 billion, maintaining a 63.88% share. Biotechnology companies follow, projected to rise from $2.44 billion to $6.23 billion as their share remains at 20.3%. Contract Manufacturing Organizations also show significant growth potential, increasing from $1.90 billion to $4.86 billion, holding a steady 15.82% share.
Fill Finish Manufacturing Market Analysis By Application
Global Fill-Finish Manufacturing Market, By Application Market Analysis (2024 - 2033)
In application segmentation, vaccines dominate with an expected market growth from $6.09 billion in 2023 to $15.57 billion by 2033, holding a 50.74% share. Oncology applications are set to grow from $2.93 billion to $7.50 billion, capturing 24.42% of the market, while autoimmune applications will expand from $1.23 billion to $3.15 billion, with a 10.26% share. Other applications are also growing from $1.75 billion to $4.48 billion, holding a 14.58% share.
Fill Finish Manufacturing Market Analysis By Region
Global Fill-Finish Manufacturing Market, By Region Market Analysis (2024 - 2033)
Regional analysis indicates that North America remains the largest market, followed closely by Europe. Asia Pacific is emerging as a significant player, driven by local demand for pharmaceuticals and biotechnological advancements. The Middle East and Africa, while nascent, are anticipated to expand rapidly with increased investment in healthcare.
Fill Finish Manufacturing Market Trends and Future Forecast
Request a custom research report for industry.
Global Market Leaders and Top Companies in Fill Finish Manufacturing Industry
Sartorius AG:
Sartorius is a leading international pharmaceutical and laboratory equipment supplier, notably involved in the manufacture of advanced fill finish solutions that enhance efficiency in biopharmaceutical production.Boehringer Ingelheim:
Boehringer Ingelheim is a global leader in contract manufacturing and offers comprehensive Fill Finish services, emphasizing innovation and quality in biopharmaceutical development.West Pharmaceutical Services:
West Pharmaceutical Services specializes in offering advanced fill finish technologies and packaging solutions, ensuring the safety and efficacy of injectables.Parexel International:
Parexel offers comprehensive services, including fill finish manufacturing, with a strong focus on regulatory compliance and operational excellence for biopharmaceuticals.Thermo Fisher Scientific:
A leading provider of laboratory services and products, Thermo Fisher also provides Fill Finish solutions that cater to the dynamic needs of the pharmaceutical industry.We're grateful to work with incredible clients.
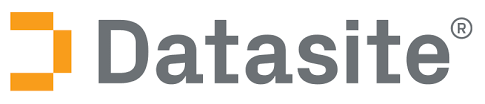
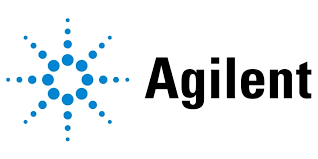

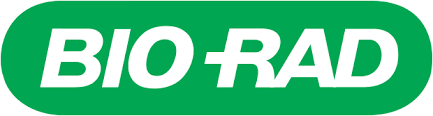
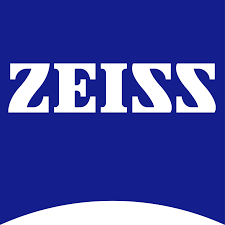
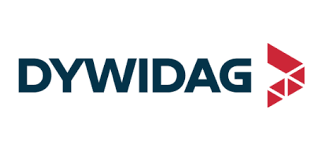
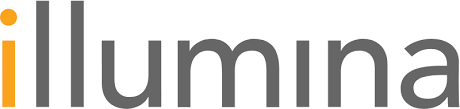

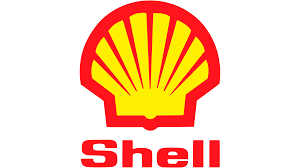
Related Industries
FAQs
What is the market size of fill Finish Manufacturing?
The fill-finish manufacturing market was valued at approximately $12 billion in 2023 and is projected to grow at a CAGR of 9.5% through 2033. This growth reflects rising demand for pharmaceuticals and biopharmaceuticals, alongside advancements in aseptic processing technologies.
What are the key market players or companies in the fill Finish Manufacturing industry?
Key players in the fill-finish manufacturing sector include major pharmaceutical and biotechnology companies, specialized contract manufacturing organizations (CMOs), and those providing aseptic processing services. These firms greatly influence market dynamics through innovations and strategic partnerships.
What are the primary factors driving the growth in the fill Finish manufacturing industry?
Growth in the fill-finish manufacturing market is driven by increasing demand for biologics, rising investments in R&D, advancements in manufacturing technologies, and compliance with stringent regulatory standards. The global health crisis also propelled the need for efficient manufacturing solutions.
Which region is the fastest Growing in the fill Finish manufacturing?
Asia Pacific is the fastest-growing region in fill-finish manufacturing, with a market growth from $2.19 billion in 2023 to $5.59 billion in 2033. This growth is fueled by expanding production capabilities and increasing investment in healthcare infrastructure.
Does ConsaInsights provide customized market report data for the fill Finish manufacturing industry?
Yes, ConsaInsights offers customized market reports tailored to specific needs and interests within the fill-finish manufacturing industry. Clients can request data segmented by region, application, or market dynamics for enhanced insights.
What deliverables can I expect from this fill Finish manufacturing market research project?
Deliverables from the fill-finish manufacturing market research project include a comprehensive report with market size and growth forecasts, competitive analysis, regional insights, and trends by segments, ensuring actionable intelligence for decision making.
What are the market trends of fill Finish manufacturing?
Current trends in fill-finish manufacturing include increased automation, greater emphasis on contract manufacturing, innovations in aseptic technologies, and a significant shift towards sustainable practices. These trends indicate evolving dynamics in the industry.