Hybrid Additive Manufacturing Machine Market Size, Share, Industry Trends and Forecast to 2033
This report provides a comprehensive analysis of the Hybrid Additive Manufacturing Machine market, offering insights into its size, growth trends, technology advancements, and regional performance over the forecast period from 2023 to 2033.
Metric | Value |
---|---|
Study Period | 2023 - 2033 |
2023 Market Size | $1.50 Billion |
CAGR (2023-2033) | 9.2% |
2033 Market Size | $3.73 Billion |
Top Companies | GE Additive, Stratasys Ltd., Materialise NV, HP Inc. |
Last Modified Date | Invalid Date |
Hybrid Additive Manufacturing Machine Market Report (2023 - 2033)
Hybrid Additive Manufacturing Machine Market Overview
What is the Market Size & CAGR of Hybrid Additive Manufacturing Machine market in 2023?
Hybrid Additive Manufacturing Machine Industry Analysis
Hybrid Additive Manufacturing Machine Market Segmentation and Scope
Request a custom research report for industry.
Hybrid Additive Manufacturing Machine Market Analysis Report by Region
Europe Hybrid Additive Manufacturing Machine Market Report:
Europe's Hybrid Additive Manufacturing Machine market is anticipated to grow from $0.43 billion in 2023 to $1.06 billion by 2033. The region's focus on sustainability and innovation makes it a significant market, with countries like Germany and the UK leading advancements in hybrid technology.Asia Pacific Hybrid Additive Manufacturing Machine Market Report:
The Asia Pacific region is witnessing significant growth in the Hybrid Additive Manufacturing Machine market, projected to rise from $0.31 billion in 2023 to $0.77 billion by 2033. Key countries like China and Japan are leading in technology adoption, capitalizing on low labor costs and an expansive manufacturing base.North America Hybrid Additive Manufacturing Machine Market Report:
North America remains a key player, with the market size expected to increase from $0.50 billion in 2023 to $1.23 billion by 2033. The strong presence of major aerospace and automotive companies is fueling demand for hybrid machines, driven by the need for precision and customization.South America Hybrid Additive Manufacturing Machine Market Report:
In South America, the market is expected to grow from $0.14 billion in 2023 to $0.34 billion in 2033. The industry's growth is facilitated by government initiatives promoting additive manufacturing technologies across various sectors.Middle East & Africa Hybrid Additive Manufacturing Machine Market Report:
The Middle East and Africa market for Hybrid Additive Manufacturing Machines is projected to grow from $0.13 billion in 2023 to $0.33 billion by 2033. Increased investments in infrastructure and technology are driving the adoption of hybrid systems in manufacturing sectors.Request a custom research report for industry.
Hybrid Additive Manufacturing Machine Market Analysis By Technology
Global Hybrid Additive Manufacturing Machine Market, By Technology Market Analysis (2024 - 2033)
The market segment analysis reveals that Material Extrusion accounts for 62.62% of the total market share in 2023, with a future projection of the same percentage in 2033. Powder Bed Fusion and Direct Energy Deposition follow with significant shares of 22% and 15.38% respectively. This distribution highlights the varying technologies' capabilities in meeting production demands.
Hybrid Additive Manufacturing Machine Market Analysis By Material
Global Hybrid Additive Manufacturing Machine Market, By Material Market Analysis (2024 - 2033)
Material utilization in the Hybrid Additive Manufacturing Machine market showcases metals as the largest segment, holding 62.62% of the market share in 2023, increasing in value significantly by 2033. Polymers and ceramics also occupy essential positions, accounting for approximately 22% and 15.38% respectively, reflecting diverse industry applications.
Hybrid Additive Manufacturing Machine Market Analysis By Application
Global Hybrid Additive Manufacturing Machine Market, By Application Market Analysis (2024 - 2033)
Applications in the aerospace and automotive sectors dominate the Hybrid Additive Manufacturing Machine market, contributing significantly to its growth. Aerospace-related applications hold a substantial market share of 57.76% in 2023, with a future forecast continuing at the same rate. Automotive applications also see growth from 20.08% share in the current forecast period. This highlights the critical role of hybrid manufacturing in sectors requiring precision and innovation.
Hybrid Additive Manufacturing Machine Market Analysis By End User
Global Hybrid Additive Manufacturing Machine Market, By End-User Industry Market Analysis (2024 - 2033)
End-user analysis shows that sectors such as aerospace, healthcare, and automotive significantly rely on Hybrid Additive Manufacturing Machines. Aerospace holds the largest segment at 57.76% market share in 2023, driven by high precision involvements in aircraft components. Automotive utilizes about 20.08%, demonstrating solid demand for hybrid technology in producing lightweight, custom parts.
Hybrid Additive Manufacturing Machine Market Analysis By Geography
Global Hybrid Additive Manufacturing Machine Market, By Geography Market Analysis (2024 - 2033)
Geographical analysis indicates North America leads the Hybrid Additive Manufacturing Machine market with a 41.02% share in 2023, growing robustly due to advanced manufacturing technologies. Europe follows closely, with about 23.21% share, and Asia Pacific at 12.31%. The distribution underscores how geographical diversity influences technology adoption and production capabilities.
Hybrid Additive Manufacturing Machine Market Trends and Future Forecast
Request a custom research report for industry.
Global Market Leaders and Top Companies in Hybrid Additive Manufacturing Machine Industry
GE Additive:
A division of General Electric, GE Additive focuses on the development of additive manufacturing technologies, providing innovative solutions for various industries including aerospace and healthcare.Stratasys Ltd.:
Stratasys is a pioneer in 3D printing technology, offering comprehensive additive manufacturing solutions that range from prototyping to full-scale production for diverse applications.Materialise NV:
Materialise specializes in 3D printing software and services, offering solutions that enhance the additive manufacturing process while ensuring high-quality outputs.HP Inc.:
HP Inc. is innovating in 3D printing technology to enable more efficient manufacturing processes, with a focus on expanding production capabilities in various industries.We're grateful to work with incredible clients.
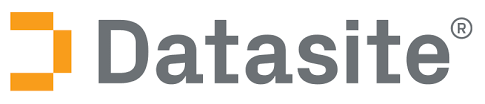
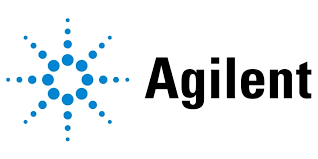

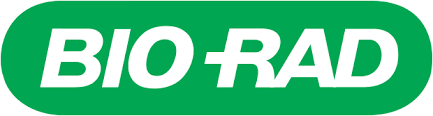
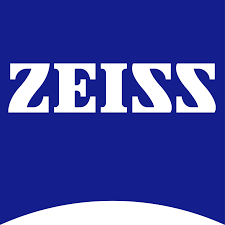
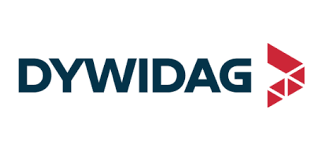
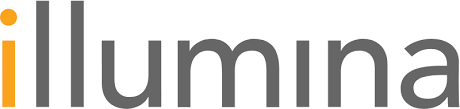

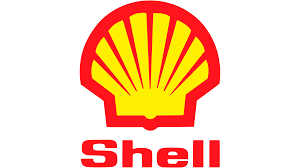
Related Industries
FAQs
What is the market size of hybrid Additive Manufacturing Machine?
The market size for hybrid additive manufacturing machines is projected to reach approximately $1.5 billion by 2033, growing at a CAGR of 9.2% from its current valuation.
What are the key market players or companies in the hybrid Additive Manufacturing Machine industry?
Key players in the hybrid additive manufacturing machine market include companies like GE Additive, Additive Industries, EOS GmbH, and Stratasys, which are at the forefront of technological advancements and market share.
What are the primary factors driving the growth in the hybrid Additive Manufacturing Machine industry?
Driving factors for growth include increased demand across sectors like aerospace and healthcare, advancements in materials technology, and enhanced efficiencies offered by hybrid additive solutions.
Which region is the fastest Growing in the hybrid Additive Manufacturing Machine market?
North America is the fastest-growing region, with a market size projected to grow from $0.62 billion in 2023 to $1.53 billion by 2033, indicating robust growth patterns.
Does ConsaInsights provide customized market report data for the hybrid Additive Manufacturing Machine industry?
Yes, ConsaInsights provides customized market reports tailored to specific needs within the hybrid additive manufacturing machine industry, ensuring relevant insights and data.
What deliverables can I expect from this hybrid Additive Manufacturing Machine market research project?
Deliverables include comprehensive market analysis, trends, forecasts, competitive landscape, and segmented data by region and application, offering valuable insights for decision-making.
What are the market trends of hybrid Additive Manufacturing Machine?
Current trends include a shift toward sustainable manufacturing solutions, increased integration of AI in production processes, and enhancements in material properties for diverse applications.