Industrial Control For Process Automation Market Size, Share, Industry Trends and Forecast to 2033
This report delves into the Industrial Control for Process Automation market, providing insights on key market dynamics, size projections, segment performance, and industry trends for the forecast period 2023-2033.
Metric | Value |
---|---|
Study Period | 2023 - 2033 |
2023 Market Size | $25.00 Billion |
CAGR (2023-2033) | 6.5% |
2033 Market Size | $47.71 Billion |
Top Companies | Siemens AG, Rockwell Automation, Schneider Electric, Honeywell , Emerson Electric |
Last Modified Date | Invalid Date |
Industrial Control For Process Automation Market Report (2023 - 2033)
Industrial Control For Process Automation Market Overview
What is the Market Size & CAGR of the Industrial Control For Process Automation market in 2023 and 2033?
Industrial Control For Process Automation Industry Analysis
Industrial Control For Process Automation Market Segmentation and Scope
Request a custom research report for industry.
Industrial Control For Process Automation Market Analysis Report by Region
Europe Industrial Control For Process Automation Market Report:
The European market is also thriving, anticipated to increase from $7.01 billion in 2023 to $13.38 billion in 2033. The focus on energy efficiency, sustainability, and regulatory compliance is pushing industries to adopt advanced automation technologies.Asia Pacific Industrial Control For Process Automation Market Report:
The Asia Pacific region is poised for substantial growth from $4.83 billion in 2023 to $9.22 billion by 2033. This rapid expansion is driven by the rising industrialization in countries like India and China, coupled with increasing foreign investments and government initiatives to promote automation and smart manufacturing.North America Industrial Control For Process Automation Market Report:
North America holds a significant portion of the market, projected to grow from $9.11 billion in 2023 to $17.38 billion in 2033. Advancements in manufacturing technologies and the adoption of smart automation solutions drive this substantial growth.South America Industrial Control For Process Automation Market Report:
In South America, the market is expected to grow from $0.82 billion in 2023 to $1.56 billion by 2033. This growth is fueled by increased investments in modernizing industrial infrastructure and growing demands from sectors like Oil and Gas.Middle East & Africa Industrial Control For Process Automation Market Report:
The Middle East and Africa market is poised to grow from $3.23 billion in 2023 to $6.17 billion in 2033, led by expanding oil, gas, and mining sectors looking to implement automation solutions to enhance efficiency and safety.Request a custom research report for industry.
Industrial Control For Process Automation Market Analysis By Technology
Global Industrial Control for Process Automation Market, By Technology Market Analysis (2024 - 2033)
The industrial control for process automation market is categorized by technology into hardware, software, and services. Hardware, which includes Distributed Control Systems (DCS), Programmable Logic Controllers (PLC), and Supervisory Control and Data Acquisition systems (SCADA), dominates the market with a significant market size of $16.81 billion in 2023, projected to double to $32.08 billion by 2033. Software solutions are also gaining traction in the market, growing from $6.81 billion in 2023 to $12.99 billion by 2033.
Industrial Control For Process Automation Market Analysis By Application
Global Industrial Control for Process Automation Market, By Application Market Analysis (2024 - 2033)
Applications of industrial control systems span across various industries, including Oil and Gas, Chemicals, Pharmaceuticals, and Food and Beverages. The Oil and Gas segment leads with a market size of $12.23 billion in 2023, set to reach $23.33 billion by 2033, driven by increasing exploration and production activities globally.
Industrial Control For Process Automation Market Analysis By Component
Global Industrial Control for Process Automation Market, By Component Market Analysis (2024 - 2033)
The market is segmented into components such as on-premise, cloud-based, and hybrid solutions. On-premise systems currently dominate the market with 67.24% market share, while the hybrid segment, accounting for 5.53% share, is gaining interest due to its flexibility and efficiency.
Industrial Control For Process Automation Market Analysis By Architecture
Global Industrial Control for Process Automation Market, By Architecture Market Analysis (2024 - 2033)
In terms of architecture, the market encompasses various structures, including centralized and distributed architectures. Centralized architectures remain predominant, providing streamlined operations and control. The distributed architecture is gaining traction, offering enhanced scalability for large enterprises.
Industrial Control For Process Automation Market Analysis By End User Industry
Global Industrial Control for Process Automation Market, By End-User Industry Market Analysis (2024 - 2033)
End-user industries such as Manufacturing, Automotive, Energy and Utilities, and Aerospace and Defense are major contributors to market growth. The Manufacturing sector leads with a market share of 48.91%, followed by Energy and Utilities at 20.6%. This trend indicates a strong reliance on automation technologies in enhancing operational efficiency.
Industrial Control For Process Automation Market Trends and Future Forecast
Request a custom research report for industry.
Global Market Leaders and Top Companies in the Industrial Control For Process Automation Industry
Siemens AG:
Siemens is a global leader in automation technology, providing advanced solutions for industrial processes. Their innovative products, including PLCs and DCS, are widely adopted across various sectors.Rockwell Automation:
Rockwell Automation specializes in industrial automation and information technology. Their solutions enhance operational efficiency and productivity, making them a key player in the industry.Schneider Electric:
Schneider Electric offers comprehensive solutions in energy management and automation, focusing on sustainability and efficiency for industrial processes.Honeywell :
Honeywell is a prominent player in automation technologies, delivering smart solutions across diverse industries, enhancing productivity and safety.Emerson Electric:
Emerson Electric provides innovative automation solutions, including process control technologies that cater to various industrial applications.We're grateful to work with incredible clients.
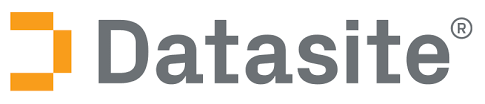
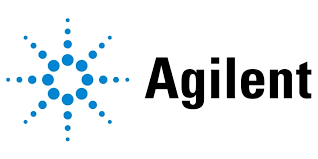

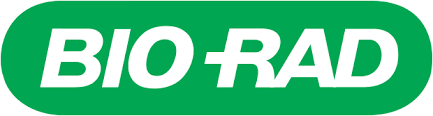
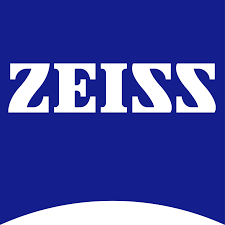
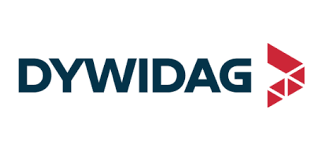
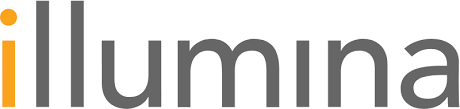

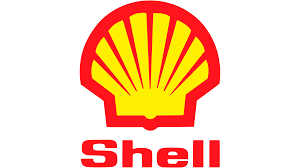
Related Industries
FAQs
What is the market size of industrial Control For Process Automation?
The industrial control for process automation market is projected to reach a value of approximately $25 billion by 2033, with a compound annual growth rate (CAGR) of 6.5%. This growth reflects the increasing demand for automation solutions across various industries.
What are the key market players or companies in this industrial Control For Process Automation industry?
Key players in the industrial control for process automation market include established companies like Siemens AG, ABB Ltd., Honeywell International Inc., Emerson Electric Co., and Rockwell Automation, Inc. These companies are recognized for their technological advancements and comprehensive solutions.
What are the primary factors driving the growth in the industrial Control For Process Automation industry?
The growth in the industrial control for process automation industry is driven by increased efficiency in manufacturing processes, the need for real-time monitoring, and the adoption of smart technologies. Moreover, regulatory requirements and the push for operational excellence further fuel market expansion.
Which region is the fastest Growing in the industrial Control For Process Automation?
Asia-Pacific is the fastest-growing region in the industrial control for process automation market, with projected growth from $4.83 billion in 2023 to $9.22 billion by 2033. This growth is attributed to rapid industrialization and technological adoption in emerging economies.
Does ConsaInsights provide customized market report data for the industrial Control For Process Automation industry?
Yes, ConsaInsights offers customized market report data tailored to the specific needs of clients in the industrial control for process automation industry, enabling deeper insights and strategic decision-making based on current market trends.
What deliverables can I expect from this industrial Control For Process Automation market research project?
From the industrial control for process automation market research project, you can expect comprehensive market analysis reports, detailed forecasts, competitive landscape assessments, and insights into regional and segment-specific trends to guide strategic initiatives.
What are the market trends of industrial Control For Process Automation?
Current market trends in industrial control for process automation include an increasing shift towards cloud-based solutions, greater integration of IoT technologies, and a focus on sustainable practices. These trends indicate a move toward smarter and greener industrial processes.