Injection Molding Machine Market Size, Share, Industry Trends and Forecast to 2033
This report provides comprehensive insights into the Injection Molding Machine market from 2023 to 2033, covering market size, growth projections, regional analysis, and competitive landscape. It highlights key trends and opportunities within the industry, aimed at assisting stakeholders in making informed investment decisions.
Metric | Value |
---|---|
Study Period | 2023 - 2033 |
2023 Market Size | $23.50 Billion |
CAGR (2023-2033) | 6.2% |
2033 Market Size | $43.54 Billion |
Top Companies | Arburg GmbH, Husky Injection Molding Systems, KraussMaffei, ENGEL Austria, Sumitomo (SHI) Demag |
Last Modified Date | Invalid Date |
Injection Molding Machine Market Report (2023 - 2033)
Injection Molding Machine Market Overview
What is the Market Size & CAGR of Injection Molding Machine market in 2023?
Injection Molding Machine Industry Analysis
Injection Molding Machine Market Segmentation and Scope
Request a custom research report for industry.
Injection Molding Machine Market Analysis Report by Region
Europe Injection Molding Machine Market Report:
The European market is anticipated to grow from $5.84 billion in 2023 to $10.82 billion by 2033. Germany and France lead the market due to their strong automotive and machinery manufacturing sectors, alongside a growing focus on sustainable production methods.Asia Pacific Injection Molding Machine Market Report:
The Asia Pacific region holds a significant share of the global injection molding machine market, valued at $4.48 billion in 2023, projected to reach $8.30 billion by 2033. The growth in this area is driven by booming manufacturing industries, particularly in countries like China, Japan, and South Korea, which are leading in automotive and consumer goods production.North America Injection Molding Machine Market Report:
North America is expected to see substantial growth from $8.63 billion in 2023 to $16.00 billion by 2033. The region is characterized by advanced technology adoption and high production standards, particularly in the automotive and medical sectors, promoting the demand for high-precision injection molding machines.South America Injection Molding Machine Market Report:
The South American market, currently valued at $1.72 billion, is projected to grow to $3.19 billion by 2033, driven by increasing investments in infrastructure and a rising demand for consumer goods. Brazil and Argentina are key markets within the region, showcasing significant potential for growth.Middle East & Africa Injection Molding Machine Market Report:
The Middle East and Africa market is projected to rise from $2.82 billion in 2023 to $5.23 billion by 2033. The market is fueled by the growing manufacturing sector in nations like South Africa and the UAE, which are increasingly investing in plastic manufacturing capabilities.Request a custom research report for industry.
Injection Molding Machine Market Analysis By Technology
Global Injection Molding Machine Market, By Technology Market Analysis (2024 - 2033)
The injection molding machine market, segmented by technology, reveals that hydraulic machines dominate the market with a share of 63.86% in 2023, valued at $15.01 billion. Electric machines cover 22.32% of the share at $5.25 billion, while other technologies comprise about 13.82% at $3.25 billion. As companies seek efficiency, the electric segment is rapidly gaining traction.
Injection Molding Machine Market Analysis By Material
Global Injection Molding Machine Market, By Material Market Analysis (2024 - 2033)
Thermoplastics lead the injection molding machine material segment, holding 63.86% of the market share valued at $15.01 billion in 2023. Thermosetting plastics and elastomers cover 22.32% and 13.82%, valued at $5.25 billion and $3.25 billion respectively. The trend towards sustainability is increasing the use of recyclable thermoplastics in manufacturing.
Injection Molding Machine Market Analysis By Application
Global Injection Molding Machine Market, By Application Market Analysis (2024 - 2033)
The automotive industry is the largest application segment, making up 58.53% of the market share at $13.75 billion in 2023. Consumer goods and medical applications follow, accounting for 22.17% and 9.39% respectively. As the demand for lightweight and high-performance components grows, the automotive sector remains a major driver for innovation in injection molding.
Injection Molding Machine Market Analysis By End User
Global Injection Molding Machine Market, By End-User Market Analysis (2024 - 2033)
The domestic market segment dominates with a share of 81.72% valued at $19.20 billion in 2023, driven by strong local manufacturing capabilities. International users account for 18.28% of the market share. The growth of the local manufacturing base enhances the reliance on injection molding processes within domestic markets.
Injection Molding Machine Market Analysis By Region Type
Global Injection Molding Machine Market, By Region Type Market Analysis (2024 - 2033)
Regional segmentation of the injection molding machine market highlights varying growth rates and market sizes. North America and Europe are mature markets, while Asia Pacific is fast-growing, benefitting from significant industrial expansion and competitive production advantages. As a result, Asia Pacific is projected as a leading market in terms of growth rate and potential through 2033.
Injection Molding Machine Market Trends and Future Forecast
Request a custom research report for industry.
Global Market Leaders and Top Companies in Injection Molding Machine Industry
Arburg GmbH:
A leading manufacturer known for innovating advanced injection molding machines focusing on precision and energy efficiency.Husky Injection Molding Systems:
Renowned for offering high-performance injection systems, Husky plays a significant role in the packaging and automotive sectors.KraussMaffei:
A prominent player offering comprehensive injection molding solutions including high-tech electric machines for various applications.ENGEL Austria:
Specializes in manufacturing advanced injection molding machines and automation solutions tailored for diverse industrial applications.Sumitomo (SHI) Demag:
Offers a wide range of precision injection molding machines, particularly well-noted for their eco-friendly electric models.We're grateful to work with incredible clients.
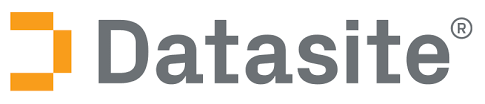
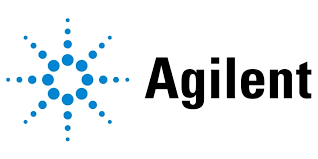

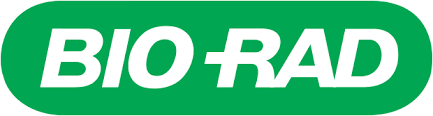
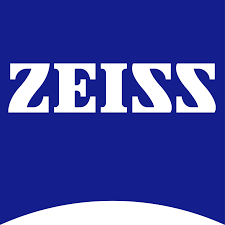
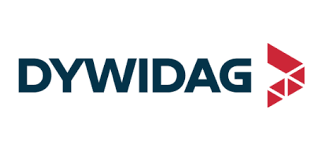
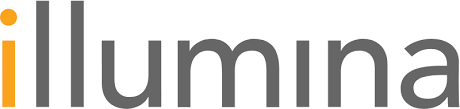

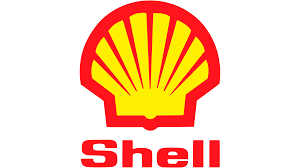
Related Industries
FAQs
What is the market size of injection Molding Machine?
The global market size for injection molding machines is projected to reach $23.5 billion by 2033, growing at a CAGR of 6.2%. This growth signals an increasing demand across various sectors, underpinning technological advancements.
What are the key market players or companies in this injection Molding Machine industry?
Key players in the injection molding machine sector include industry giants such as Arburg, Engel, and Haitian International. Their innovative approaches and diverse product offerings significantly influence market dynamics and competitive landscape.
What are the primary factors driving the growth in the injection Molding Machine industry?
The growth in the injection molding machine industry is primarily driven by increasing demand for lightweight and durable materials, adoption of automation technologies, and expanding applications across automotive, consumer goods, and electronics sectors.
Which region is the fastest Growing in the injection Molding Machine?
The Asia Pacific region is forecasted as the fastest-growing market for injection molding machines. Market size is expected to grow from $4.48 billion in 2023 to $8.30 billion by 2033, fueled by industrial growth and manufacturing expansion.
Does ConsaInsights provide customized market report data for the injection Molding Machine industry?
Yes, ConsaInsights offers customized market report data tailored to specific requirements in the injection molding machine industry, enabling stakeholders to make informed decisions based on targeted research and insights.
What deliverables can I expect from this injection Molding Machine market research project?
Expect comprehensive deliverables from the project, including detailed market analysis, growth projections, competitive landscape assessments, and actionable insights into regional performance and segment data.
What are the market trends of injection Molding Machine?
Key market trends include rising adoption of electric injection molding machines, increased focus on sustainable practices, and ongoing technological advancements aimed at enhancing efficiency and product quality in manufacturing.