Metal Casting Market Size, Share, Industry Trends and Forecast to 2033
This report provides a comprehensive analysis of the Metal Casting market, focusing on current trends, market size, and future forecasts from 2023 to 2033. Insights include market segmentation, regional analysis, and key players' contributions to the industry.
Metric | Value |
---|---|
Study Period | 2023 - 2033 |
2023 Market Size | $123.40 Billion |
CAGR (2023-2033) | 5.6% |
2033 Market Size | $215.50 Billion |
Top Companies | Nemak, Alcoa Corporation, PCC Structurals, Grede Holdings LLC, Aalberts Industries |
Last Modified Date | Invalid Date |
Metal Casting Market Report (2023 - 2033)
Metal Casting Market Overview
What is the Market Size & CAGR of Metal Casting market in 2023?
Metal Casting Industry Analysis
Metal Casting Market Segmentation and Scope
Request a custom research report for industry.
Metal Casting Market Analysis Report by Region
Europe Metal Casting Market Report:
The European market is expected to grow from USD 33.52 billion in 2023 to USD 58.53 billion by 2033. Europe places a strong focus on sustainable practices and innovation in casting, with considerable investment in technologies that reduce waste and enhance performance in industries like automotive and energy.Asia Pacific Metal Casting Market Report:
In the Asia Pacific region, the Metal Casting market is growing robustly, expected to expand from USD 23.66 billion in 2023 to USD 41.31 billion by 2033. Factors driving this growth include rapid industrialization, a surge in automotive production, and a strong emphasis on infrastructure development in countries like China and India.North America Metal Casting Market Report:
North America is anticipated to see significant growth in the Metal Casting market, increasing from USD 46.00 billion in 2023 to USD 80.34 billion by 2033. The automotive industry is a major contributor to this growth, alongside advancements in manufacturing technologies and a rise in aerospace applications.South America Metal Casting Market Report:
South America's Metal Casting market is projected to grow from USD 11.01 billion in 2023 to USD 19.22 billion by 2033. The region faces challenges such as economic instability but is expected to benefit from increasing investments in renewable energy and mining sectors, promoting demand for cast metal products.Middle East & Africa Metal Casting Market Report:
In the Middle East and Africa, the Metal Casting market is projected to grow from USD 9.22 billion in 2023 to USD 16.10 billion by 2033, driven by an increased focus on infrastructure projects, oil and gas investments, and mining activities that require high-quality metal components.Request a custom research report for industry.
Metal Casting Market Analysis By End User
Global Metal Casting Market, By End-User Industry Market Analysis (2024 - 2033)
The automotive sector emerges as the largest end-user, projected to grow from USD 55.16 billion in 2023 to USD 96.33 billion by 2033. This sector significantly drives the demand for cast components such as engine blocks and transmission cases. The aerospace industry follows, with growth from USD 25.61 billion to USD 44.72 billion, reflecting the increasing need for durable, lightweight parts. The construction segment is also vital, with its market expanding from USD 12.86 billion to USD 22.45 billion, reflecting infrastructure developments globally.
Metal Casting Market Analysis By Material Type
Global Metal Casting Market, By Material Type Market Analysis (2024 - 2033)
Ferrous metals dominate the market, expected to grow from USD 82.27 billion in 2023 to USD 143.67 billion by 2033. The versatility and mechanical properties of ferrous alloys make them suitable for various applications. Non-ferrous metals are also gaining traction, alongside traditional materials, expected to rise from USD 32.22 billion to USD 56.27 billion due to enhanced properties like corrosion resistance and lightweight characteristics.
Metal Casting Market Analysis By Casting Process
Global Metal Casting Market, By Casting Process Market Analysis (2024 - 2033)
Traditional casting techniques remain predominant, accounting for USD 102.10 billion in 2023, and are projected to reach USD 178.30 billion by 2033, highlighting their established use in many industries. However, advanced casting techniques are starting to capture market share, with growth from USD 21.30 billion to USD 37.19 billion, driven by increased demand for precision parts and complex geometries.
Metal Casting Market Analysis By Application
Global Metal Casting Market, By Application Market Analysis (2024 - 2033)
The application segment reveals a strong growth trajectory, especially in component manufacturing, rising from USD 64.93 billion to USD 113.40 billion, evidencing the need for customized components across various sectors. Energy & Power, and Equipment Manufacturing applications are also notable, with expected growth supporting the overall market expansion.
Metal Casting Market Analysis By Technology
Global Metal Casting Market, By Technology Market Analysis (2024 - 2033)
Ongoing technological advancements are reshaping the landscape of metal casting. Technologies like 3D printing and advanced simulation techniques are enhancing productivity, accuracy, and reducing operational costs, pushing the market towards sustainable practices.
Metal Casting Market Trends and Future Forecast
Request a custom research report for industry.
Global Market Leaders and Top Companies in Metal Casting Industry
Nemak:
A leading provider of advanced aluminum components for the automotive industry, Nemak is known for its innovative processes and sustainable practices.Alcoa Corporation:
With expertise in aluminum production and casting, Alcoa operates globally, supplying a range of sectors including aerospace and automotive.PCC Structurals:
Specializing in investment casting and advanced manufacturing processes, PCC Structurals provides high-performance components for aerospace and industrial sectors.Grede Holdings LLC:
Grede is a major player in the metal casting industry, delivering iron and aluminum castings primarily for automotive, energy, and industrial markets.Aalberts Industries:
Aalberts is an innovative manufacturing company focusing on advanced mechanical and thermal processes that include metal casting solutions.We're grateful to work with incredible clients.
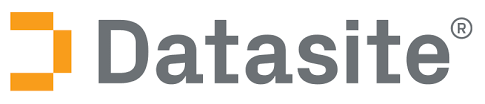
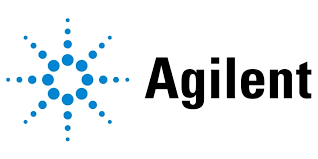

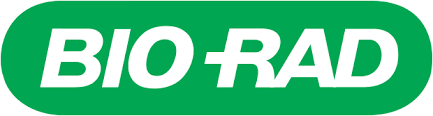
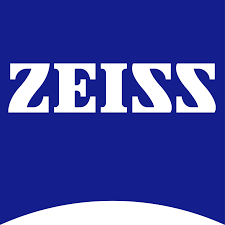
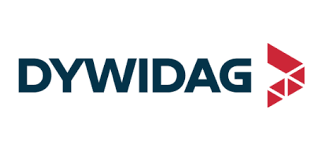
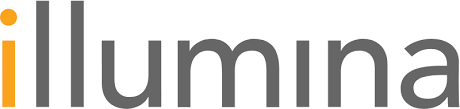

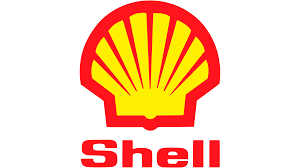
Related Industries
FAQs
What is the market size of metal Casting?
The global metal-casting market is projected to reach approximately $123.4 billion by 2033, growing at a CAGR of 5.6%. The market continues to expand due to the increasing demand for cast metal products across diverse industries.
What are the key market players or companies in this metal Casting industry?
Key players in the metal-casting industry include companies like Alcoa Corporation, Ductile Iron, Foundry Technologies LLC, and Precision Castparts Corp. They focus on innovation and efficiency in manufacturing, catering to the automotive and aerospace markets primarily.
What are the primary factors driving the growth in the metal Casting industry?
Growth in the metal-casting industry is propelled by rising automotive production, advances in casting technologies, and the increasing popularity of electric vehicles, which require advanced metal components. Additionally, infrastructure development boosts demand across sectors.
Which region is the fastest Growing in the metal Casting?
The North American region is anticipated to be the fastest-growing market segment, projected to grow from $46.00 billion in 2023 to $80.34 billion by 2033, driven by increased demand in automotive and industrial machinery sectors.
Does ConsaInsights provide customized market report data for the metal Casting industry?
Yes, ConsaInsights offers customized market report data for the metal-casting industry. Clients can request tailored analytics and market insights according to specific segments or regions, ensuring precise decision-making capabilities.
What deliverables can I expect from this metal Casting market research project?
Deliverables from the metal-casting market research project include comprehensive reports, market data analytics, segmentation analysis, growth forecasts, and key insights on competitive players, trends, and regional developments.
What are the market trends of metal Casting?
Current market trends in metal-casting include a shift towards advanced casting techniques, rising investments in green casting technologies, and a focus on sustainability. Additionally, the integration of digital technologies is enhancing production efficiency.