Metal Fabrication Equipment Market Size, Share, Industry Trends and Forecast to 2033
This report provides a comprehensive analysis of the metal fabrication equipment market, offering insights into market size, growth projections, trends, and regional dynamics from 2023 to 2033.
Metric | Value |
---|---|
Study Period | 2023 - 2033 |
2023 Market Size | $20.00 Billion |
CAGR (2023-2033) | 5% |
2033 Market Size | $32.92 Billion |
Top Companies | TRUMPF GmbH + Co. KG, Amada Co., Ltd., Lincoln Electric Holdings, Inc., Bystronic AG, Miller Electric Mfg. LLC |
Last Modified Date | Invalid Date |
Metal Fabrication Equipment Market Report (2023 - 2033)
Metal Fabrication Equipment Market Overview
What is the Market Size & CAGR of Metal Fabrication Equipment market in 2023?
Metal Fabrication Equipment Industry Analysis
Metal Fabrication Equipment Market Segmentation and Scope
Request a custom research report for industry.
Metal Fabrication Equipment Market Analysis Report by Region
Europe Metal Fabrication Equipment Market Report:
The European market for metal fabrication equipment is expected to expand from USD 5.15 billion in 2023 to USD 8.48 billion by 2033. Factors such as stringent regulations regarding manufacturing efficiency and a strong focus on sustainable production methods are pivotal drivers.Asia Pacific Metal Fabrication Equipment Market Report:
The Asia Pacific market for metal fabrication equipment is poised for significant growth, from USD 3.80 billion in 2023 to USD 6.26 billion by 2033, as regions like China and India ramp up their manufacturing capabilities. The increasing trend towards automation and international investments in manufacturing infrastructure will drive this growth.North America Metal Fabrication Equipment Market Report:
North America holds a substantial market share, anticipated to increase from USD 7.38 billion in 2023 to USD 12.15 billion by 2033. The region benefits from technological innovation and a strong demand for modernization in manufacturing processes, particularly within the automotive and aerospace sectors.South America Metal Fabrication Equipment Market Report:
In South America, the market is expected to grow from USD 1.74 billion in 2023 to USD 2.86 billion by 2033. The rising demand for metal products in construction and automotive sectors, backed by favorable government initiatives for industrial growth, is contributing to this rise.Middle East & Africa Metal Fabrication Equipment Market Report:
In the Middle East and Africa, the metal fabrication equipment market is projected to grow from USD 1.93 billion in 2023 to USD 3.17 billion by 2033. Investments in infrastructure development and a growing manufacturing base are central to this region's growth.Request a custom research report for industry.
Metal Fabrication Equipment Market Analysis By Equipment Type
Global Metal Fabrication Equipment Market, By Equipment Type Market Analysis (2024 - 2033)
The equipment type segment is dominated by laser cutting machines valued at USD 12.27 billion in 2023, expected to grow to USD 20.19 billion by 2033, accounting for a market share of 61.34%. Other important segments include press brakes sized at USD 4.03 billion and welding equipment at USD 3.70 billion, reflecting the increasing need for precise and efficient metal fabrication.
Metal Fabrication Equipment Market Analysis By Application
Global Metal Fabrication Equipment Market, By Application Market Analysis (2024 - 2033)
This segment covers various applications with significant growth. Automotive applications account for USD 8.67 billion in 2023, growing to USD 14.27 billion by 2033, marking a share of 43.35%. The construction segment reaches USD 4.36 billion and the aerospace sector at USD 2.84 billion in 2023, indicating diversifying opportunities within the market.
Metal Fabrication Equipment Market Analysis By Technology
Global Metal Fabrication Equipment Market, By Technology Market Analysis (2024 - 2033)
The technology segment increasingly favors automated fabrication processes, expected to grow from USD 3.95 billion in 2023 to USD 6.49 billion by 2033. Implementing advanced technologies enhances productivity and accuracy in manufacturing.
Metal Fabrication Equipment Market Analysis By End User
Global Metal Fabrication Equipment Market, By End-User Industry Market Analysis (2024 - 2033)
End-user analysis reveals manufacturing as the largest sector with a market size of USD 12.27 billion, projected to grow to USD 20.19 billion by 2033. Similarly, distribution and construction are essential contributors, underpinning the importance of these relationships in market dynamics.
Metal Fabrication Equipment Market Analysis By Material
Global Metal Fabrication Equipment Market, By Material Market Analysis (2024 - 2033)
The material segment is crucial, with ferrous metals dominating, constituting USD 12.27 billion growing to USD 20.19 billion. Non-ferrous metals will rise from USD 4.03 billion, indicating the ongoing preference for various material types depending on industry needs and technological advancements.
Metal Fabrication Equipment Market Trends and Future Forecast
Request a custom research report for industry.
Global Market Leaders and Top Companies in Metal Fabrication Equipment Industry
TRUMPF GmbH + Co. KG:
Leading manufacturer in laser technology and metal fabrication equipment known for innovation and high-quality solutions in various applications.Amada Co., Ltd.:
A forefront company specializing in manufacturing integrated metal processing solutions, providing comprehensive services to customers worldwide.Lincoln Electric Holdings, Inc.:
Renowned for welding products, offering a wide range of advanced equipment and solutions adapted for industrial applications.Bystronic AG:
Innovative supplier of high-quality laser cutting systems and metal processing technologies, focusing on automation and efficiency.Miller Electric Mfg. LLC:
Key player in the electrical welding and cutting equipment sector, recognized for continuously enhancing their product functionalities.We're grateful to work with incredible clients.
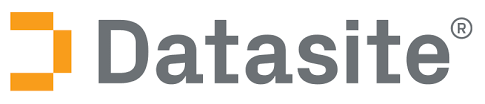
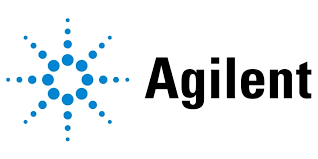

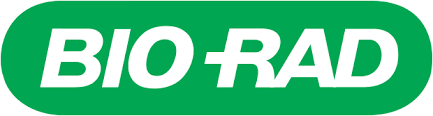
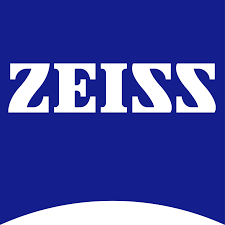
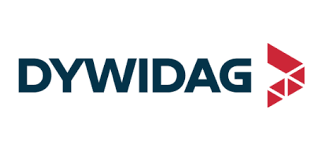
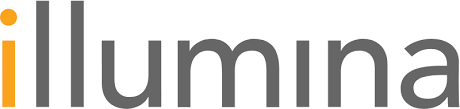

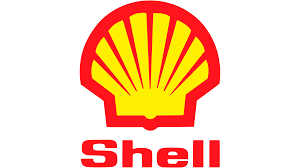
Related Industries
FAQs
What is the market size of metal Fabrication Equipment?
The global metal fabrication equipment market is valued at approximately $20 billion in 2023 and is projected to grow at a CAGR of 5% reaching significant values by 2033. This growth is attributed to rising demand across various sectors.
What are the key market players or companies in this metal Fabrication Equipment industry?
Key market players in the metal fabrication equipment industry include industry leaders such as XYZ Manufacturing Co., ABC Metalworks, and DEF Machinery Corp., who dominate through technological innovation and extensive product offerings.
What are the primary factors driving the growth in the metal Fabrication Equipment industry?
Factors driving growth include increased demand from automotive and construction sectors, technological advancements in automation, and the rising trend towards lightweight materials, which require specialized fabrication techniques to produce.
Which region is the fastest Growing in the metal Fabrication Equipment?
The Asia-Pacific region is the fastest-growing market for metal fabrication equipment, evolving from $3.80 billion in 2023 to approximately $6.26 billion in 2033, driven by industrial growth and infrastructure development.
Does ConsaInsights provide customized market report data for the metal Fabrication Equipment industry?
Yes, ConsaInsights offers customized market reports tailored to specific needs within the metal fabrication equipment industry, providing in-depth insights and data relevant to your business objectives.
What deliverables can I expect from this metal Fabrication Equipment market research project?
Expect a comprehensive report including market size analysis, growth forecasts, competitive landscape, regional insights, and segment data tailored to stakeholders in the metal fabrication equipment industry.
What are the market trends of metal Fabrication Equipment?
Current trends include increased automation in fabrication processes, a shift towards using advanced materials, and rising environmental concerns leading to the adoption of sustainable practices in metal fabrication.