Powder Injection Molding Pim Market Size, Share, Industry Trends and Forecast to 2033
This report provides a comprehensive analysis of the Powder Injection Molding (PIM) market, covering the current market landscape, size forecasts, regional insights, and emerging trends between 2023 and 2033.
Metric | Value |
---|---|
Study Period | 2023 - 2033 |
2023 Market Size | $5.60 Billion |
CAGR (2023-2033) | 6.5% |
2033 Market Size | $10.69 Billion |
Top Companies | Höganäs AB, Kyocera Corporation, LPW Technology Ltd, ExOne Company |
Last Modified Date | Invalid Date |
Powder Injection Molding Pim Market Report (2023 - 2033)
Powder Injection Molding Pim Market Overview
What is the Market Size & CAGR of Powder Injection Molding Pim market in 2023?
Powder Injection Molding Pim Industry Analysis
Powder Injection Molding Pim Market Segmentation and Scope
Request a custom research report for industry.
Powder Injection Molding Pim Market Analysis Report by Region
Europe Powder Injection Molding Pim Market Report:
The European PIM market was valued at USD 1.40 billion in 2023, expected to grow to USD 2.67 billion by 2033. The region’s focus on high-quality manufacturing and stringent regulations in production processes promote the use of PIM technology.Asia Pacific Powder Injection Molding Pim Market Report:
In the Asia Pacific region, the PIM market was valued at USD 1.12 billion in 2023, projected to double to USD 2.14 billion by 2033. This growth is attributed to the booming automotive and electronics sectors, coupled with rising investments in modernization and infrastructure.North America Powder Injection Molding Pim Market Report:
In North America, the market size was USD 2.13 billion in 2023, anticipated to reach USD 4.07 billion by 2033. The strong presence of key players in the automotive and aerospace industries contributes notably to this expansion.South America Powder Injection Molding Pim Market Report:
The South American market for PIM was valued at USD 0.21 billion in 2023 and is expected to grow to USD 0.40 billion by 2033. Increasing demand for consumer goods and industrial components is driving growth in this region, alongside foreign investments.Middle East & Africa Powder Injection Molding Pim Market Report:
In the Middle East and Africa, the PIM market is valued at USD 0.74 billion in 2023, projected to grow to USD 1.41 billion by 2033. This growth is facilitated by increasing manufacturing capabilities and a burgeoning middle class demanding consumer goods.Request a custom research report for industry.
Powder Injection Molding Pim Market Analysis By Product
Global Powder Injection Molding (PIM) Market, By Product Type Market Analysis (2024 - 2033)
The Metal Powder segment dominated the PIM market with a size of USD 3.81 billion in 2023, projected to reach USD 7.26 billion by 2033, holding a significant 67.95% share of the market. Ceramic Powder follows with a market size of USD 1.47 billion in 2023, expanding to USD 2.80 billion by 2033 (26.21% share). Polymer Powder remains smaller, with expected growth from USD 0.33 billion to USD 0.62 billion, representing a 5.84% share.
Powder Injection Molding Pim Market Analysis By Application
Global Powder Injection Molding (PIM) Market, By Application Market Analysis (2024 - 2033)
Automotive applications are the leading segment, contributing USD 2.34 billion in 2023, expanding to USD 4.46 billion by 2033 (41.78% share). Healthcare applications, accounting for USD 1.18 billion, are projected to grow to USD 2.26 billion (21.15% share). Other applications include Electronics and Aerospace and Defense, illustrating the diverse applicability of PIM technology.
Powder Injection Molding Pim Market Analysis By End User
Global Powder Injection Molding (PIM) Market, By End-User Industry Market Analysis (2024 - 2033)
Key end-user industries include Automotive (41.78% share) and Healthcare (21.15%). With increasing demand for high-quality components and devices in these sectors, PIM is optimizing production timelines and reducing costs across several verticals, which enhances overall market growth.
Powder Injection Molding Pim Market Analysis By Technology
Global Powder Injection Molding (PIM) Market, By Technology Market Analysis (2024 - 2033)
The PIM market is segmented into High-Pressure Injection (USD 2.89 billion to USD 5.51 billion) and Low-Pressure Injection (USD 1.32 billion to USD 2.51 billion) technologies, reflecting the advantages of each in different manufacturing contexts. High-Pressure Injection retains a dominant share (51.56%) due to its suitability for dense materials.
Powder Injection Molding Pim Market Analysis By Region Development
Global Powder Injection Molding (PIM) Market, By Development Stage Market Analysis (2024 - 2033)
The market showcases differentiation between established markets and developing regions. Established markets exhibit high adoption of advanced PIM technologies, while developing regions focus on scaling capabilities and improving industry standards, encouraging the integration of PIM techniques.
Powder Injection Molding Pim Market Trends and Future Forecast
Request a custom research report for industry.
Global Market Leaders and Top Companies in Powder Injection Molding Pim Industry
Höganäs AB:
A leading global supplier of metal powders and developer of innovative solutions for PIM technology.Kyocera Corporation:
Specializes in high technological components and is heavily invested in the PIM process for ceramic applications.LPW Technology Ltd:
Renowned for its advanced metal powder solutions and contributions to increasing PIM efficiency.ExOne Company:
Pioneering additive manufacturing solutions, significantly contributing to the PIM segment with technology solutions.We're grateful to work with incredible clients.
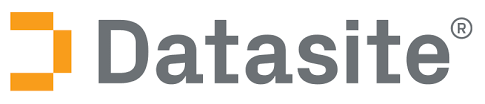
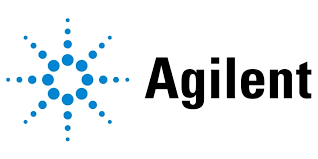

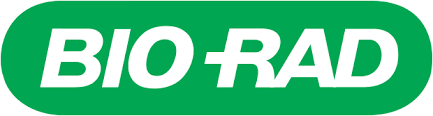
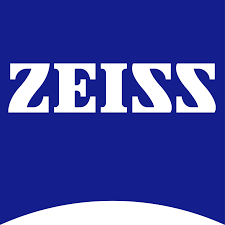
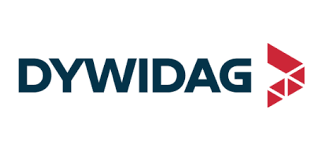
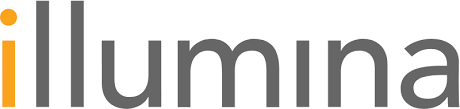

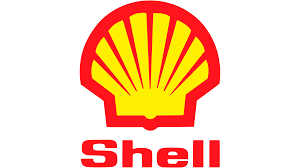
Related Industries
FAQs
What is the market size of Powder Injection Molding (PIM)?
The global Powder Injection Molding market is valued at approximately $5.6 billion in 2023, with a projected compound annual growth rate (CAGR) of 6.5% over the next decade, indicating significant expansion in various sectors.
What are the key market players or companies in the Powder Injection Molding (PIM) industry?
Key players in the Powder Injection Molding industry include Wellman, Höganäs, and ExOne, which drive innovation and competitive strategies, enhancing market dynamics in the global landscape.
What are the primary factors driving the growth in the Powder Injection Molding (PIM) industry?
Major growth drivers include increasing demand for lightweight materials in automotive and aerospace applications, advancements in PIM technology, and rising investments in R&D, enabling efficiency and cost reduction in manufacturing.
Which region is the fastest Growing in the Powder Injection Molding (PIM)?
The Asia-Pacific region is expected to exhibit rapid growth, expanding from $1.12 billion in 2023 to $2.14 billion by 2033, due to industrialization and rising demand for high-performance materials.
Does ConsaInsights provide customized market report data for the Powder Injection Molding (PIM) industry?
Yes, ConsaInsights offers tailored market reports, providing precise insights and data specific to the Powder Injection Molding industry to assist organizations in making informed decisions.
What deliverables can I expect from this Powder Injection Molding (PIM) market research project?
Deliverables include comprehensive reports with market analysis, forecasts, competitive landscape evaluations, and segment data crucial for strategic planning in the Powder Injection Molding sector.
What are the market trends of Powder Injection Molding (PIM)?
Current trends indicate a shift towards automation in manufacturing processes, an increase in sustainable powder materials, and rising applications in diverse sectors like healthcare, automotive, and consumer goods.