Powder Metallurgy Market Size, Share, Industry Trends and Forecast to 2033
This market report provides a comprehensive analysis of the Powder Metallurgy landscape, focusing on trends, market size, forecast data from 2023 to 2033, segmentation, and regional insights that inform industry stakeholders of current opportunities and challenges.
Metric | Value |
---|---|
Study Period | 2023 - 2033 |
2023 Market Size | $10.30 Billion |
CAGR (2023-2033) | 6.8% |
2033 Market Size | $20.24 Billion |
Top Companies | Kennametal Inc., PMI Powder Metallurgy Inc., GKN Powder Metallurgy |
Last Modified Date | Invalid Date |
Powder Metallurgy Market Report (2023 - 2033)
Powder Metallurgy Market Overview
What is the Market Size & CAGR of Powder Metallurgy market in 2023?
Powder Metallurgy Industry Analysis
Powder Metallurgy Market Segmentation and Scope
Request a custom research report for industry.
Powder Metallurgy Market Analysis Report by Region
Europe Powder Metallurgy Market Report:
Europe's Powder Metallurgy market is projected to increase from $3.32 billion in 2023 to $6.52 billion by 2033. Countries such as Germany, the UK, and France spearhead this growth through investments in high-performance materials, alongside a strong automotive industry focus on reducing vehicle weight.Asia Pacific Powder Metallurgy Market Report:
In the Asia Pacific region, the Powder Metallurgy market was valued at $1.80 billion in 2023 and is projected to reach $3.53 billion by 2033, indicating robust growth driven by industrial expansion, increasing automotive production, and advancements in materials technology. Key players in countries like China and Japan are heavily investing in R&D to enhance production efficiency.North America Powder Metallurgy Market Report:
In North America, the market size is expected to expand from $3.79 billion in 2023 to $7.44 billion by 2033. The automotive sector plays a pivotal role here, supported by innovations in lightweight materials and enhanced manufacturing technologies. Collaborations with technology firms are also facilitating advancements in PM processes.South America Powder Metallurgy Market Report:
The South American Powder Metallurgy market is anticipated to grow from $0.97 billion in 2023 to $1.91 billion by 2033. This growth is fueled by increasing investments in industrialization and infrastructure projects, particularly in Brazil and Argentina, where the demand for advanced manufacturing solutions is rising.Middle East & Africa Powder Metallurgy Market Report:
The Middle East and Africa PM market is estimated to grow from $0.43 billion in 2023 to $0.84 billion by 2033. Efforts to diversify economies and enhance manufacturing capabilities are driving investments in PM technologies, with countries like South Africa leading the way.Request a custom research report for industry.
Powder Metallurgy Market Analysis By Material
Global Powder Metallurgy Market, By Material Market Analysis (2024 - 2033)
The Powder Metallurgy market, segmented by material, reveals Ferrous Materials leading with a size of $6.49 billion in 2023 and expected to reach $12.75 billion by 2033. Non-Ferrous Materials follow, growing from $2.88 billion to $5.66 billion. The demand for Exotic Materials is comparatively niche, currently at $0.93 billion but aiming for $1.83 billion as specialty applications grow.
Powder Metallurgy Market Analysis By Application
Global Powder Metallurgy Market, By Application Market Analysis (2024 - 2033)
The market segmented by applications indicates Automotive as a leading sector, contributing $4.59 billion in 2023 and projected to reach $9.02 billion in 2033. Electronics and Healthcare are significant, too, showing steady growth influenced by the need for precision components and medical devices.
Powder Metallurgy Market Analysis By Process
Global Powder Metallurgy Market, By Process Market Analysis (2024 - 2033)
In terms of processes, Sintering technology dominates the market with a size of $8.63 billion in 2023, expected to grow to $16.97 billion. Powder Processing is also notable, witnessing an increase from $1.67 billion to $3.28 billion, driven by innovations to optimize production efficiency.
Powder Metallurgy Market Analysis By End User
Global Powder Metallurgy Market, By End-User Industry Market Analysis (2024 - 2033)
The analysis by end-user industry shows significant contributions from Automotive, Healthcare, and Aerospace. The Automotive sector leads with $4.59 billion in 2023 and anticipated growth to $9.02 billion, while Aerospace, Electronics, and Healthcare sectors also display positive trends, indicating a broader acceptance of PM technologies.
Powder Metallurgy Market Analysis By Technology
Global Powder Metallurgy Market, By Technology Market Analysis (2024 - 2033)
Various technologies in the Powder Metallurgy market are experiencing growth driven by advancements such as additive manufacturing and advanced sintering techniques. As industries seek more sophisticated solutions, the demand for new technologies continues to expand, promising enhanced product capabilities and efficiencies.
Powder Metallurgy Market Trends and Future Forecast
Request a custom research report for industry.
Global Market Leaders and Top Companies in Powder Metallurgy Industry
Kennametal Inc.:
A key player in the tooling and materials science sector, Kennametal develops integrated, precise, and durable powder metallurgy solutions used across various industries.PMI Powder Metallurgy Inc.:
Specializes in the production of high-quality powdered metals and components, leading advancements in the PM industry through innovative manufacturing processes.GKN Powder Metallurgy:
A leading global supplier, GKN specializes in the manufacture of precision components through PM processes, focusing on automotive and industrial applications.We're grateful to work with incredible clients.
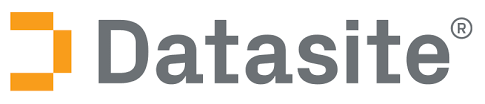
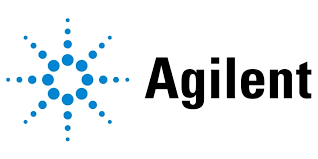

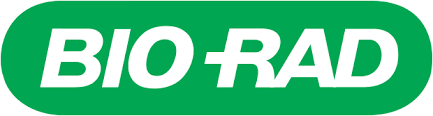
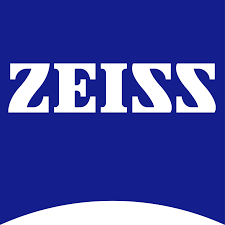
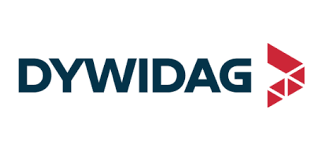
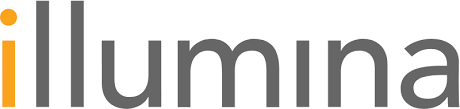

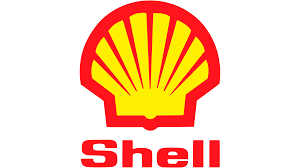
Related Industries
FAQs
What is the market size of powder metallurgy?
The global powder metallurgy market is valued at approximately $10.3 billion in 2023 and is projected to grow at a CAGR of 6.8%, reaching around $18.8 billion by 2033. This growth reflects increasing demand across various sectors.
What are the key market players or companies in the powder metallurgy industry?
Key players in the powder metallurgy industry include renowned corporations such as GKN Powder Metallurgy, Hitachi Chemical Co., Ltd., and AMETEK Inc. These companies leverage advanced manufacturing technologies to enhance product offerings and sustain market presence.
What are the primary factors driving the growth in the powder metallurgy industry?
The growth in the powder metallurgy industry is driven by increasing demand for lightweight materials in automotive and aerospace sectors, advancements in manufacturing technologies, and a rising focus on energy efficiency and sustainability in production processes.
Which region is the fastest Growing in the powder metallurgy market?
The Asia-Pacific region is currently the fastest-growing segment of the powder metallurgy market. Its market size is expected to increase from $1.80 billion in 2023 to $3.53 billion by 2033, driven by industrialization and technological advancements.
Does ConsaInsights provide customized market report data for the powder metallurgy industry?
Yes, ConsaInsights offers customizable market report data tailored to specific needs within the powder metallurgy industry. Clients can request bespoke analyses focusing on particular segments, regions, or trends for optimal decision-making.
What deliverables can I expect from this powder metallurgy market research project?
Deliverables from a powder metallurgy market research project typically include comprehensive reports, in-depth analysis of market trends and segments, competitive landscape evaluations, and forecasts outlining potential growth trajectories and opportunities.
What are the market trends of powder metallurgy?
Current trends in the powder metallurgy market include increased adoption of advanced powder processing techniques, a growing emphasis on sustainability, and expanding applications in the healthcare and consumer products sectors, enhancing market diversification.