Precast Prefabricated Construction Market Size, Share, Industry Trends and Forecast to 2033
This detailed market report covers the Precast Prefabricated Construction industry, offering insights on market size, trends, segmentation, and forecasts from 2023 to 2033. It analyses regional markets and identifies key players, providing a comprehensive overview of current conditions and future potential.
Metric | Value |
---|---|
Study Period | 2023 - 2033 |
2023 Market Size | $100.00 Billion |
CAGR (2023-2033) | 6.5% |
2033 Market Size | $190.83 Billion |
Top Companies | Buzzi Unicem, LafargeHolcim, CRH plc, Prefabricated Construction Systems, LLC, Eagle Roofing Products |
Last Modified Date | Invalid Date |
Precast Prefabricated Construction Market Report (2023 - 2033)
Precast Prefabricated Construction Market Overview
What is the Market Size & CAGR of Precast Prefabricated Construction market in 2023?
Precast Prefabricated Construction Industry Analysis
Precast Prefabricated Construction Market Segmentation and Scope
Request a custom research report for industry.
Precast Prefabricated Construction Market Analysis Report by Region
Europe Precast Prefabricated Construction Market Report:
In Europe, the market is set to increase from 26.93 billion USD in 2023 to 51.39 billion USD by 2033. The region’s focus on sustainability and innovation in construction technologies enhances the demand for precast solutions. Additionally, favorable regulations supporting energy-efficient construction are propelling the industry's growth in countries like Germany, France, and the UK.Asia Pacific Precast Prefabricated Construction Market Report:
The Asia Pacific region is witnessing rapid growth, with the market size projected to rise from 19.86 billion USD in 2023 to 37.90 billion USD by 2033. Factors driving this growth include urbanization, government initiatives promoting infrastructural development, and an increasing focus on disaster-resilient buildings. Key markets in this region include China, India, and Australia, where investments in smart city projects are prevalent.North America Precast Prefabricated Construction Market Report:
North America stands as a significant market, anticipated to expand from 33.93 billion USD in 2023 to 64.75 billion USD by 2033. The region’s growth is driven by a surge in residential and commercial construction activities alongside governmental support for sustainable building practices. The demand for precast elements in earthquake-prone areas is also on the rise, as they offer superior structural performance.South America Precast Prefabricated Construction Market Report:
In South America, the market is expected to grow from 9.59 billion USD in 2023 to 18.30 billion USD in 2033. This growth is primarily driven by increased infrastructural development projects, alongside a rising demand for affordable housing solutions that utilize precast methods for efficiency and cost-effectiveness. Strategic alliances between private developers and local governments are anticipated to further boost the market.Middle East & Africa Precast Prefabricated Construction Market Report:
The Middle East and Africa market is projected to grow from 9.69 billion USD in 2023 to 18.49 billion USD by 2033. The increasing investments in infrastructural improvements and development projects, particularly in the Gulf region, support this growth. The construction of hotels, commercial real estate, and large-scale infrastructure projects necessitates the adoption of precast technology to meet modern building standards.Request a custom research report for industry.
Precast Prefabricated Construction Market Analysis By Product
Global Precast-Prefabricated Construction Market, By Product Market Analysis (2024 - 2033)
The market is divided into components, modules, and infrastructure elements. Components dominate the market, estimated to increase from 62.31 billion USD in 2023 to 118.91 billion USD by 2033. Modules are gaining traction, projected to grow from 26.19 billion USD in 2023 to 49.98 billion USD by 2033.
Precast Prefabricated Construction Market Analysis By Application
Global Precast-Prefabricated Construction Market, By Application Market Analysis (2024 - 2033)
The key applications of precast prefabricated construction include residential, commercial, and industrial sectors. Residential construction is the largest segment, anticipated to grow from 57.64 billion USD in 2023 to 110.00 billion USD by 2033, reflecting the enduring demand for housing solutions. Commercial construction and industrial projects will also see significant growth, estimated to rise from 23.04 billion USD to 43.97 billion USD and from 9.90 billion USD to 18.89 billion USD, respectively.
Precast Prefabricated Construction Market Analysis By Technology
Global Precast-Prefabricated Construction Market, By Technology Market Analysis (2024 - 2033)
Technological advancements in precast construction focus on digital fabrication techniques and automation. The market for advanced technology is growing, with size estimates increasing from 26.19 billion USD in 2023 to 49.98 billion USD within the same timeframe, significantly impacting cost and efficiency.
Precast Prefabricated Construction Market Analysis By End User
Global Precast-Prefabricated Construction Market, By End-User Market Analysis (2024 - 2033)
The market is largely driven by builders, real estate developers, and public sector projects. Builders hold a significant share at 57.64 billion USD, expected to rise sharply by 2033. Real estate developers are also key players, projected to grow from 23.04 billion USD to 43.97 billion USD, while government and municipal projects are anticipated to grow to 18.89 billion USD.
Precast Prefabricated Construction Market Analysis By Financing
Global Precast-Prefabricated Construction Market, By Financing Type Market Analysis (2024 - 2033)
The financing landscape is changing with predominant models being public, private, and mixed financing. Public financing leads the market at 62.31 billion USD, while private finance is also significant, expected to increase from 26.19 billion USD to 49.98 billion USD, reflecting changing attitudes towards construction funding.
Precast Prefabricated Construction Market Trends and Future Forecast
Request a custom research report for industry.
Global Market Leaders and Top Companies in Precast Prefabricated Construction Industry
Buzzi Unicem:
Buzzi Unicem is a leading company in precast concrete, recognized for its innovative solutions in construction materials and technologies.LafargeHolcim:
As a global leader in building materials, LafargeHolcim integrates precast construction methods to provide sustainable construction solutions across various markets.CRH plc:
CRH is one of the world's largest building materials businesses, with a strong presence in precast concrete practices and a commitment to sustainable development.Prefabricated Construction Systems, LLC:
This company specializes in sophisticated precast concrete products designed for modern construction challenges, effectively improving construction timelines.Eagle Roofing Products:
Eagle Roofing Products is known for high-quality precast components within the roofing market, focusing on durability and design.We're grateful to work with incredible clients.
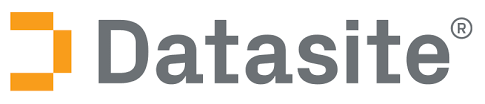
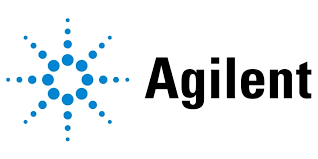

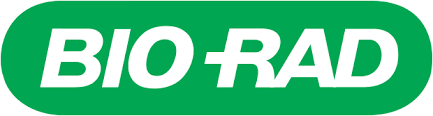
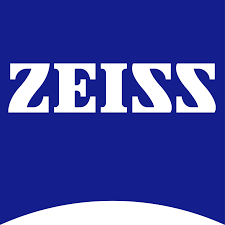
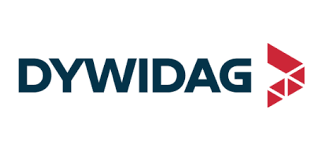
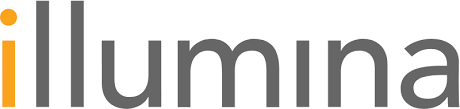

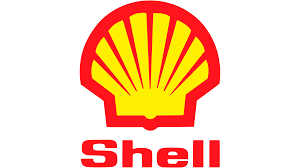
Related Industries
FAQs
What is the market size of precast Prefabricated Construction?
The precast-prefabricated construction market is projected to reach approximately $100 billion by 2033, growing at a CAGR of 6.5% from a base market size of $100 billion in 2023.
What are the key market players or companies in this precast Prefabricated Construction industry?
Key players in the precast-prefabricated construction industry include major construction firms, precast product manufacturers, and developers focusing on innovative building methods, ensuring efficiency and sustainability.
What are the primary factors driving the growth in the precast Prefabricated Construction industry?
Growth in this industry is driven by increasing demand for faster construction timelines, reduced labor costs, and enhanced resource efficiency through advanced technologies and sustainability practices.
Which region is the fastest Growing in the precast Prefabricated Construction?
North America is the fastest-growing region in the precast-prefabricated construction market, projected to grow from $33.93 billion in 2023 to $64.75 billion by 2033, reflecting significant demand for efficient construction.
Does ConsaInsights provide customized market report data for the precast Prefabricated Construction industry?
Yes, ConsaInsights offers tailored market report data for the precast-prefabricated construction industry, allowing clients to obtain insights specific to their business needs and strategic goals.
What deliverables can I expect from this precast Prefabricated Construction market research project?
Deliverables include comprehensive market analysis reports, segmentation data, forecasts, competitive landscape overviews, and actionable insights to inform strategic decisions.
What are the market trends of precast Prefabricated Construction?
Current trends highlight the adoption of automation, digital fabrication techniques, and a shift towards sustainability in materials and methods, shaping the future of precast-prefabricated construction.